Données physico-chimiques
Données atomiques
Numéro atomique |
Masse atomique |
Configuration électronique |
Structures cristallines |
Rayon métallique pour la coordinence 12 |
25 |
54,94 g.mol-1 |
[Ar] 3d5 4s2 |
alpha jusqu’à 700°C,
bêta jusqu’à 1 088°C,
gamma jusqu’à 1139°C puis delta.
- forme alpha, cubique centrée de paramètre
a = 0,893 nm
|
130 pm |
Données physiques
Masse volumique |
Dureté |
Température de fusion |
Température d’ébullition |
Conductibilité électrique |
Conductibilité thermique |
Solubilité dans l’eau |
7,20 g.cm-3 |
6,0 |
1 244°C |
1 962°C |
0,695.106 S.m-1 |
7,82 W.m-1.K-1 |
décomposé |
Données chimiques
Électronégativité
de Pauling |
pKa : Mnaq2+/MnOH+aq |
pKa :
HMnO4/MnO4–aq |
pKs : Mn(OH)2 |
pKs : Mn(OH)3 |
pKs : Mn(OH)4 |
pKs : MnS |
1,55 |
10,6 |
-2,2 |
12,7 |
36 |
56 |
9,5 |
Potentiels standards :
MnO42- + e = MnO43- |
E°= -0,27 V |
MnO4– + 8H+ + 5e = Mn2+ + 4H2O |
E° = 1,51 V |
Mn2+ + 2e = Mn(s) |
E°= -1,17 V |
MnVI + 2e = MnIV |
E°= 0,44 V |
2MnO2(s) + 2H+ + 2e = Mn2O3(s) + H2O |
E° = 1,04 V |
MnO4– + 4H+ + 3e = MnO2(s) + 2H2O |
E° = 1,68 V |
MnO4– + 2H2O + 3e = MnO2(s) + 4OH– |
E° = 0,59 V |
MnO4– + e = MnO42- |
E° = 0,57 V |
MnIV + e = MnIII |
E°= 1,64 V |
MnIII + e = MnII |
E°= 1,49 V |
MnO2(s) + 4H+ + 2e = Mn2++ 2H2O |
E° = 1,33 V |
Données thermodynamiques
Manganèse cristallisé
- Entropie molaire standard à 298,15 K : S° = 32 J.K-1mol-1
- Capacité thermique molaire sous pression constante à 298,15 K : Cp° = 26,3 J.K-1mol-1
- Enthalpie molaire standard de fusion à la température de fusion : 14,6 kJ.mol-1
- Enthalpie molaire standard d’ébullition à la température d’ébullition : 244,8 kJ.mol-1
|
Manganèse gazeux
- Enthalpie molaire standard de formation à 298,15 K : 280,8 kJ.mol-1
- Enthalpie libre molaire standard de formation à 298,15 K : 238,6 kJ.mol-1
- Entropie molaire standard à 298,15 K : S° = 173,7 J.K-1mol-1
- Capacité thermique molaire sous pression constante à 298,15 K : Cp° = 20,8 J.K-1mol-1
|
Données industrielles
Matières premières
La teneur moyenne de l’écorce terrestre est de 0,1 %.
Minerais
On trouve le manganèse (Mn) dans les principaux minerais suivants :
- la pyrolusite (MnO2),
- le psilomélane (oxyde hydraté),
- l’hausmannite (Mn3O4),
- la rhodochrocite (MnCO3),
- la rhodonite (MnSiO3).
Le manganèse est souvent associé à des minerais de fer.
Les minerais dits métallurgiques qui ont des teneurs qui dépassent 35 % de Mn sont destinés à la fabrication d’alliages. Les minerais riches ont des teneurs supérieures à 44 % de Mn et qui peuvent atteindre 57 %. Les minerais ferrifères qui ont des teneurs comprises entre 10 et 35 % de Mn et les minerais manganifères qui sont des minerais de fer riches en Mn (5 à 10 %), sont employés pour ajuster la teneur en manganèse des fontes produites au haut fourneau.
En 2019, exprimé en Mn contenu, les minerais riches, avec une teneur ≥ à 44 % de Mn, représentent 39 % de la production totale de minerais, les intermédiaires avec une teneur comprise entre 30 et 44 %, 48 % de la production, les pauvres, avec une teneur inférieure à 30 %, 13 % de la production.
Teneurs moyennes des minerais extraits dans les principaux pays producteurs :
% Mn
Australie |
37-53 % |
|
Inde |
10-54 % |
Brésil |
33-51 % |
|
Kazakhstan |
35-36 % |
Chine |
20-30 % |
|
Malaisie |
32-45 % |
Gabon |
45-53 % |
|
Afrique du Sud |
30-48 % |
Ghana |
28-34 % |
|
Ukraine |
30-35 % |
Source : USGS
Productions minières
Le production minière mondiale s’élevait, en 2019, à 20,1 millions de t de Mn contenu.
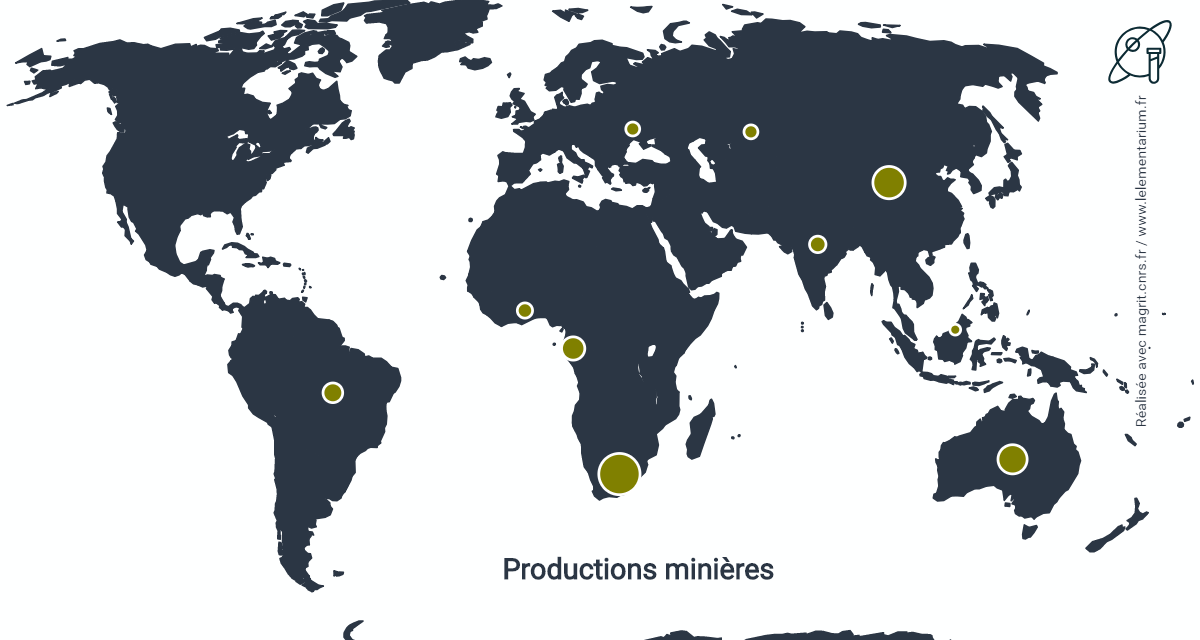
en milliers de t de Mn contenu
Afrique du Sud |
6 900 |
|
Chine |
1 300 |
Australie |
3 100 |
|
Inde |
800 |
Gabon |
2 500 |
|
Ukraine |
400 |
Brésil |
1 500 |
|
Malaisie |
300 |
Ghana |
1 500 |
|
Kazakhstan |
200 |
Source : Eramet
Principales mines
En 2019.
en milliers de t de minerai produit
Groote Eylandt (Australie) |
5 582 |
|
Nchwaning et Gloria (Afrique du Sud) |
3 409 |
Hotazel (Afrique du Sud) |
4 936 |
|
Farm Perth (Afrique du Sud) |
2 800 |
Nsuta (Ghana) |
4 800 |
|
Thembeka Myedi (Afrique du Sud) |
2 500 |
Moanda (Gabon) |
4 765 |
|
Farm York (Afrique du Sud) |
1 300 |
Tshipi Borwa (Afrique du Sud) |
3 640 |
|
Azul (Brésil) |
1 000 |
Sources : rapports des sociétés
- Groote Eylandt, dans le Territoire du Nord, en Australie, est la mine de manganèse à haute teneur, la plus importante au monde. Elle est exploitée, à ciel ouvert, par GEMCO, joint venture entre South32 (ex BHP Billiton) 60 % et Anglo American 40 %. En 2019, la production est de 5,582 millions de t. Les réserves prouvées et probables sont de 65 millions de t renfermant 43 % de Mn.
- Au Ghana, la mine de Nsuta est exploitée par le groupe chinois Ningxia Tianyuan Manganese Industry (TMI) qui a acquis, en mai 2017, la société Ghana Manganese Company détenue à 90 % par le groupe australien Consolidated Minerals Ltd (Consmin) avec une production, en 2018, de 4,8 millions de t d‘un minerai de carbonate de manganèse avec des réserves de 46,9 millions de t de minerai renfermant 27,9 % de Mn.
- Au Gabon, la mine de manganèse de Moanda, exploitée par Comilog (Compagnie minière de l’Ogooué), filiale à 63,71 % d’Eramet avec une participation de 28,7 % de l’État gabonais, produit un minerai de teneur élevée, comprise entre 45 et 50 % avec une moyenne de 46 %. Le minerai, extrait à ciel ouvert (la couche de stérile ne possède qu’une épaisseur de 4 à 5 m), à l’aide de pelles hydrauliques, est enrichi sur place dans une laverie, acheminé par bande transporteuse jusqu’à la gare de Moanda puis transporté sur 648 km par le Transgabonais (dont Comilog possède la concession pendant 30 ans depuis 2005) jusqu’au port d’Owendo, près de Libreville. La production, en 2019, est de 4,765 millions de t de minerai avec 2,5 millions de t de Mn contenu. La France, les États-Unis et le Japon sont les principaux importateurs du manganèse gabonais dont la plus grande partie est utilisée sous forme de ferroalliage. Les réserves prouvées et probables sont, au 1er janvier 2020, de 210 millions de t de minerai à 45,3 % de Mn.
- En Afrique du Sud, les mines sont concentrées dans le bassin du Kalahari avec :
- Les mines de Hotazel Manganese Mines (HMM), à ciel ouvert, de Mamatwan et souterraine de Wessels qui sont exploitées à 44,4 % par South32 (ex BHP Billiton) et 29,6 % par Anglo American qui ont produit, en 2019, 4,936 millions de t de minerai, avec des réserves prouvées et probables de 130 millions de t renfermant 40 % de Mn.
- Les mines souterraines de Nchwaning et Gloria exploitées par Assmang, avec en 2019, une production de 3,409 millions de t de minerai et des réserves prouvées et probables pour Nchwaning de 177,9 millions de t renfermant 43 % de Mn et pour Gloria de 115 millions de t renfermant 37,4 % de Mn.
- La mine de Thembeka Myedi exploitée souterrainement par Kalagadi Manganese, avec une production de 3 millions de t/an.
- La mine de Tshipi Borwa, à ciel ouvert, exploitée par Tshipi é Ntle Manganese Mining détenu à 50,1 % par Main Street 774 et 49,9 % par le groupe australien Jupiter Mines avec des exportations, en 2019, de 3,5 millions de t et des réserves prouvées et probables de 92 millions de t renfermant 36,32 % de Mn.
- La mine de Farm Perth exploitée par United Manganese of Kalahari (UMK) détenu à 51 % par Majestic Silver Trading et 49 % par le groupe russe Renova, possède des réserves de 112 millions de t.
- La mine de Farm York exploitée par Kudumane Manganese Resources détenu à 49 % par le groupe Asia Minerals avec une capacité de production de 1,8 million de t/an.
- Au Brésil, à Carajás (État de Pará), en Amazonie, Vale exploite à ciel ouvert la mine Azul avec une production, en 2019, de 1,0 million de t de minerai et des réserves prouvées et probables de 13,1 millions de t de minerai à 26,8 % de Mn.
Principaux producteurs
En 2019, les principaux producteurs étaient :
Sources : rapports des sociétés
- South32 (ex BHP Billiton) : 5,536 millions de t de minerai en 2019 dont 3,349 millions de t en Australie et 2,187 millions de t en Afrique du Sud. Possède 60 % de la société Samancor Manganese (avec 40 % pour Anglo American) qui détient, en Afrique du Sud, 74 % de la mine à ciel ouvert de Mamatwan et de la mine souterraine de Wessels dans le bassin du Kalahari. Possède, en Australie, 60 % (avec 40 % pour le groupe Anglo American) de la mine de Groote Eyland.
- Ningxia Tianyuan Manganese Industry (TMI) a acquis, en mai 2017, la société australienne Consolidated Minerals Ltd (Consmin) qui possédait, au Ghana, 90 % de la société Ghana Manganese Company qui exploite un gisement de carbonate de manganèse dans la mine de Nsuta avec des réserves de 46,9 millions de t de minerai renfermant 27,9 % de Mn et exploitait la mine à ciel ouvert de Woodie Woodie située dans la région de Pilbara, en Australie de l’Ouest avec une capacité de production de 1,5 million de t/an et des réserves de 21,8 millions de t de minerai à 30,2 % de Mn.
- Eramet (Gabon) : production de 4,765 millions tonnes de minerai, en 2019, dans la mine de Moanda.
- Assmang Ltd (Afrique du Sud) détenu à 50 % par African Rainbow Minerals (ARM) et 50 % par Assore : 3,409 millions de t de minerai, en 2019.
- Anglo American : possède 40 % de Samancor Manganese, en Afrique du Sud et 40 % de la production de GEMCO qui exploite la mine de Groote Eyland. La production, en 2019, est de 3,513 millions de t de minerai.
- Compania Minera Autlan (Mexique), a produit, en 2017, dans l’état d’Hidalgo, 1,390 million de t avec les mines de Molango et Naopa et du dioxyde naturel de manganèse, dans la mine de Nonoalco, avec 14 000 t, destinées principalement à la fabrication de piles.
- Vale (Brésil) : 1,6 million de t de minerai en 2019 avec la mine d’Azul, la mine à ciel ouvert de Morro da Mina dans l’État de Minas Gerais avec une production en 2019 de 200 000 t et des réserves de 8,3 millions de t de minerai renfermant 26,8 % de Mn et la mine souterraine d’Urucum, dans l’État du Mato Grosso do Sul avec une production de 0,4 million de t en 2019 et des réserves prouvées et probables, en 2017, de 9,3 millions de t renfermant 46,5 % de Mn.
Commerce international : en 2019.
Les exportations ont porté sur un total de 40,008 millions de t de minerai ou concentrés de teneur supérieure à 20 % de Mn avec comme principaux pays exportateurs :
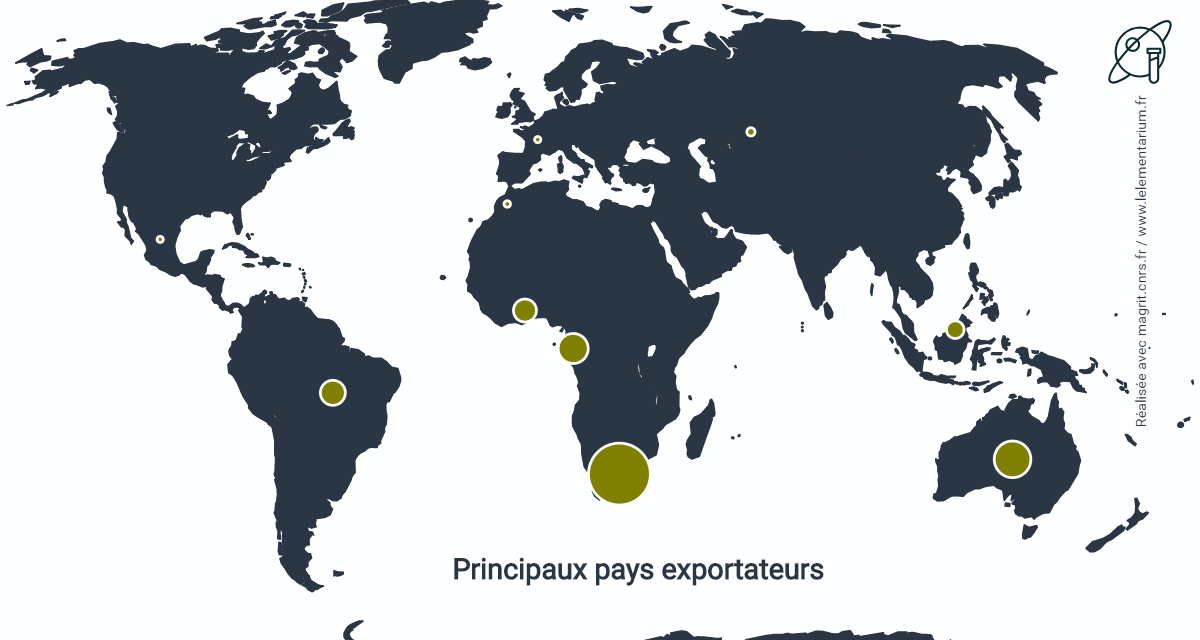
en milliers de t de minerai
Afrique du Sud |
19 690 |
|
Brésil |
3 783 |
Australie |
6 803 |
|
Malaisie |
2 052 |
Gabon |
5 591 |
|
Côte d’Ivoire |
1 228 |
Ghana |
5 028 |
|
Birmanie |
1 075 |
Source : ITCLes exportations d’Afrique du Sud sont destinées à :
- 69 % à la Chine,
- 9 % à l’Inde,
- 4 % à la Malaisie.
Principaux pays importateurs sur un total mondial de 45,091 millions de t :
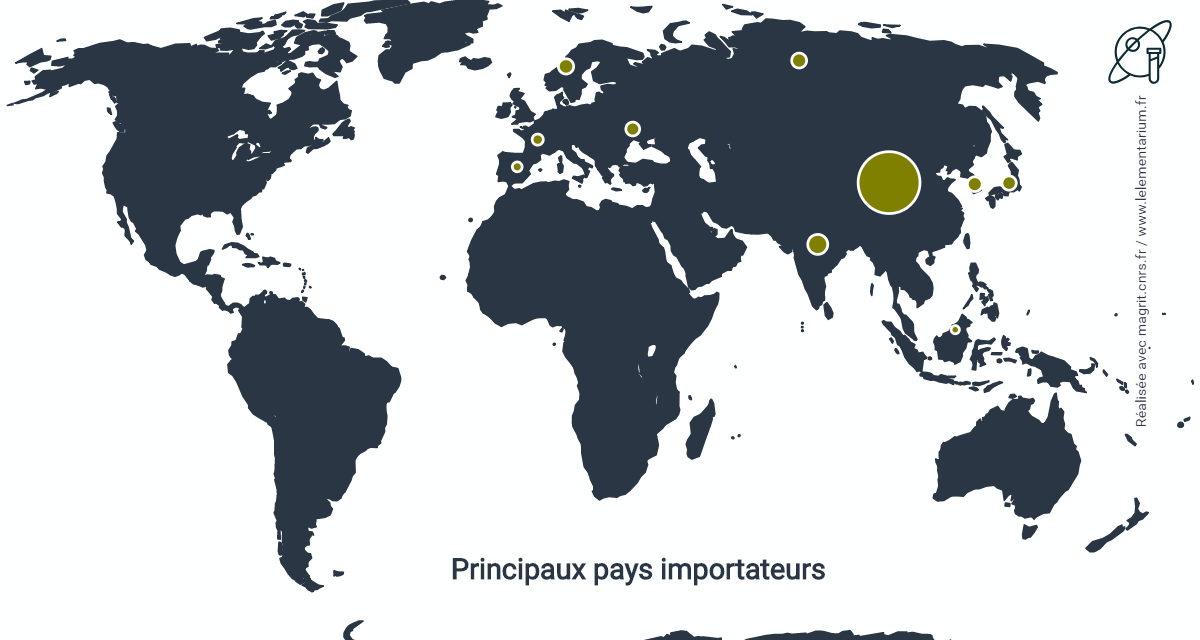
en milliers de t de minerai
Chine |
34 175 |
|
Japon |
1 039 |
Inde |
2 854 |
|
Corée du Sud |
1 009 |
Norvège |
1 217 |
|
France |
482 |
Malaisie |
1 204 |
|
États-Unis |
434 |
Russie |
1 081 |
|
Espagne |
275 |
Source : ITCLes importations chinoises proviennent à :
- 39 % d’Afrique du Sud,
- 15 % d’Australie,
- 15 % du Ghana,
- 11 % du Gabon,
- 9 % du Brésil.
Réserves
Les réserves mondiales de minerais riches (Mn > 44 %) étaient, en 2019, de 810 millions de t.
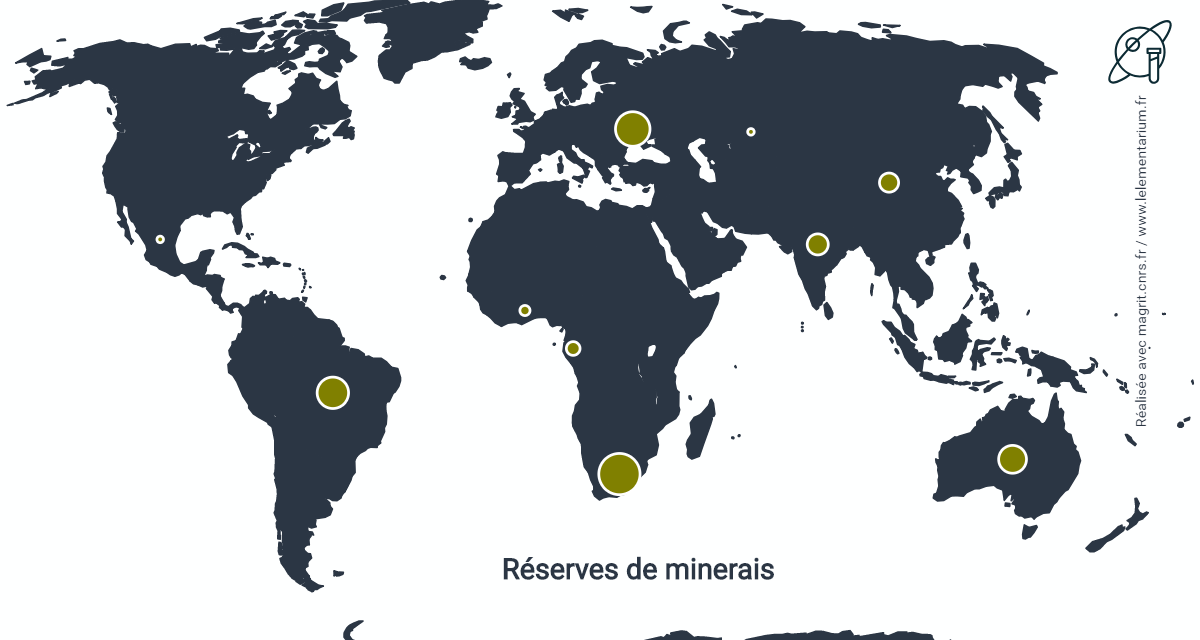
en milliers de t de Mn contenu
Afrique du Sud |
260 000 |
|
Chine |
54 000 |
Ukraine |
140 000 |
|
Inde |
34 000 |
Brésil |
140 000 |
|
Ghana |
13 000 |
Australie |
100 000 |
|
Kazakhstan |
5 000 |
Gabon |
61 000 |
|
Mexique |
5 000 |
L’Afrique du Sud possède le gisement de manganèse le plus important au monde. Il est situé dans le désert du Kalahari, dans la région d’Hotazel, dans la province du Cap du Nord. Il couvre une superficie de plus de 1 100 km2. C’est un dépôt sédimentaire, formé entre 2,2 et 2,6 milliards d’années, constitué de 3 couches riches en manganèse, les teneurs sont comprises entre 20 et 48 % de Mn, situé entre 30 et 110 m de profondeur. La première couche a 10 m d’épaisseur en moyenne, la seconde 0,5 à 3 m et la troisième, de 6 à 45 m, cette dernière étant la plus exploitée. Ces couches sont séparées par des couches de minerais de fer dénommées BIF (Banded Iron formation). Ce gisement a été découvert en 1906 et commencé à être exploité à compter de 1942. Il a été exceptionnellement préservé de l’érosion.
Nodules sous-marins : le manganèse avec des teneurs comprises entre 15 et 30 % est associé à du cuivre, du nickel et de cobalt. Les réserves sont estimées à 2,3 milliards de t de Mn contenu. Leur exploitation n’est pas actuellement rentable.
Métallurgie
Des minerais de manganèse sont directement utilisés en sidérurgie ou dans le cas de la pyrolusite dans les piles sèches (voir plus loin) mais, le plus souvent, les minerais sont réduits pour donner des ferromanganèse et ferrosilicomanganèse. Le manganèse métallique n’a pas d’utilisation finale hors comme élément d’alliages.
Ferroalliages
Il existe deux méthodes pour obtenir des ferromanganèse et ferrosilicomanganèse, avec une part de plus en plus importante de la production à l’aide de fours électriques :
Dans un haut fourneau (7 % de la production), principalement en Chine.
La métallurgie du manganèse s’apparente à celle de la fonte, sauf que la réduction de MnO (oxyde stable au-dessus de 1 200°C) par CO est plus difficile que celle de FeO. Contrairement à FeO, MnO est réduit par le carbone. On considère que la réduction ne peut se produire qu’au-dessus de 1310°C et peut être représentée par une réaction voisine de :
3 MnO + 4 C = Mn3C + 3 CO
En présence du fer présent dans le minerai, il se forme un carbure mixte fer – manganèse. Une partie du manganèse, sous forme de MnO, reste dans le laitier. Cette filière permet l’obtention :
- du ferromanganèse carburé : composition : Mn : 76-80 %, Fe : 12-15 %, C < 7,5 %, Si < 1,2 %. Il est au manganèse ce que la fonte est au fer.
- du ferromanganèse affiné (à moyen carbone) : Mn 80 %, et contient de 1 à 1,5 % de C. Il est produit le plus souvent par affinage à l’oxygène du ferromanganèse carburé.
Dans un four électrique (93 % de la production).
Le ferromanganèse est obtenu en chauffant un mélange de minerai de manganèse renfermant de d’oxyde de manganèse MnO2 avec de l’oxyde de fer (III) Fe2O3 et du carbone. Cette filière permet également, avec l’ajout de silice, l’obtention :
- du ferrosilicomanganèse : composition moyenne : Mn : 65-68 %, Si : 16-21 %, Fe : 10 %, C : 1,5-2 %.
- du ferromanganèse surraffiné (à bas carbone) : Mn de 80 à 90 %, C : ~ 0,1 %. Il est produit à partir de ferrosilicomanganèse.
Métal
Il est obtenu par électrolyse de solutions aqueuses de sulfate manganeux et sulfate d’ammonium qui donne du manganèse (dénommé EMM) à 99,98 % de teneur en manganèse, sous forme de fragments de cathodes appelés « flakes » ou électrothermiquement, à la limite d’affinage du ferromanganèse qui donne du manganèse à 99 % de teneur avec une teneur en carbone inférieure à 0,02 %. L’utilisation de l’aluminothermie pour l’obtention du métal est réalisée en Ukraine.
Procédé hydrométallurgique employé par Comilog à Moanda, au Gabon : le minerai étant constitué principalement de dioxyde de manganèse, MnO2, qui n’est pas soluble dans l’acide sulfurique employé, en général, dans les procédés hydrométallurgiques, il est nécessaire de le réduire pour former MnO qui est soluble. Cette réduction est réalisée après ajout de coke, dans un four électrique tournant, à 950°C. La dissolution du minerai réduit est effectuée par lixiviation dans l’acide sulfurique. Une première purification par neutralisation et passage en milieu basique permet d’éliminer, au travers d’un filtre-presse, sous forme d’hydroxydes, le fer et l’aluminium présents en solution. Une deuxième purification, concernant les autres ions métalliques, Zn2+, Cu2+, Co2+, Ni2+, Cd2+, présents en plus faible quantité, est réalisée par sulfuration, précipitation des sulfures correspondants et nouvelle filtration dans un filtre-presse. La solution de sulfate de manganèse purifiée est électrolysée sous un courant de 30 000 A à l’aide de 140 cuves d’électrolyse, comportant chacune 40 cathodes en acier inoxydable et 41 anodes. Toutes les 32 heures, les cathodes sont déchargées et le métal déposé récupéré sous forme de « flakes » de 2 à 3 mm d’épaisseur avec une pureté de 99,7 % de Mn.
Schéma de la production (document du Complexe Métallurgique de Moanda)
Recyclage
Le manganèse contenu dans les ferrailles est recyclé avec ces dernières. Le dioxyde de manganèse des piles est également, en partie, recyclé.
Production d’alliages de manganèse
Cette production est directement liée à celle de l’acier, la consommation moyenne de manganèse étant, en 2019, de 6 à 7 kg par tonne d’acier. A l’exception du Japon qui a développé l’introduction directe, en sidérurgie, de minerai de manganèse, l’apport de manganèse est réalisé, sous forme métallique, à l’aide d’alliages.
Productions
en milliers de t d’alliages et %, en 2019
|
Total |
Ferrosilico-manganèse |
Ferromanganèse carburé |
Ferromanganèse affiné |
Total |
23 887 |
18 026 |
4 432 |
1 429 |
Chine |
14 700 |
69 % |
39 % |
38 % |
Inde |
2 400 |
11 % |
16 % |
6 % |
Ukraine |
900 |
4 % |
3 % |
|
Japon |
700 |
|
8 % |
8 % |
Norvège |
600 |
2 % |
|
17 % |
Corée du Sud |
600 |
1 % |
4 % |
12 % |
Russie |
600 |
2 % |
4 % |
|
Afrique du Sud |
400 |
1 % |
3 % |
6 % |
Sources : Eramet et IMnI
En 2019, sur une production mondiale d’alliages de manganèse de 23,9 millions de t, le ferrosilicomanganèse représente 76 % de la production, le ferromanganèse carburé 28 % et le ferromanganèse affinés 6 %. En 2015, la production de l’Union européenne, principalement en Espagne et en France, est de 579 000 t dont 259 000 t de ferrosilicomanganèse, 298 000 t de ferromanganèse carburé et 21 800 t de ferromanganèse affiné. Par ailleurs, en Europe, la production de la Norvège est importante avec, en 2019, 600 000 t.
La production de manganèse métal (EMM) est très majoritairement réalisée en Chine, par électrolyse, avec, en 2019, une production de 1,53 million de t sur un total mondial de 1,62 million de t. Les autres pays producteurs sont l’Afrique du Sud, avec Manganese Metal Company, l’Ukraine avec Zaporozhye, l’Indonésie avec Qingshan et le Gabon avec Eramet. En 2018, les exportations chinoises ont porté sue 408 000 t.
Commerce international
Principaux pays exportateurs, en 2019 :
- Inde : 699 000 t de ferrosilicomanganèse.
- Ukraine : 505 000 t de ferrosilicomanganèse, 97 000 t de ferromanganèse carburé.
- Malaisie : 299 000 t de ferrosilicomanganèse, 319 000 t de ferromanganèse carburé.
- Afrique du Sud : 120 000 t de ferrosilicomanganèse, 150 000 t de ferromanganèse carburé, 83 000 t de ferromanganèse affiné.
- Norvège : 288 000 t de ferrosilicomanganèse.
Principaux pays importateurs : en 2019 :
- États-Unis : 370 000 t de ferrosilicomanganèse, 211 000 t de ferromanganèse carburé, 125 000 t de ferromanganèse affiné.
- Allemagne : 228 000 t de ferrosilicomanganèse, 122 000 t de ferromanganèse carburé, 35 000 t de ferromanganèse affiné.
- Japon : 280 000 t de ferrosilicomanganèse, 103 000 t de ferromanganèse carburé.
- Pays Bas : 151 000 t de ferrosilicomanganèse, 100 000 t de ferromanganèse carburé, 96 000 t de ferromanganèse affiné.
- Italie : 207 000 t de ferrosilicomanganèse, 84 000 t de ferromanganèse carburé, 25 000 t de ferromanganèse affiné.
- Turquie : 198 000 de ferrosilicomanganèse, 54 000 t de ferromanganèse carburé, 39 000 t de ferromanganèse affiné.
Producteurs
Les principaux producteurs, hors producteurs chinois, sont les suivants :
- Eramet a produit, en 2019, 740 000 t d’alliages de manganèse dont 271 000 t de silicomanganèse, 83 000 t de ferroalliages carburés et 386 000 t de ferroalliages affinés. La production a été réalisée dans des fours électriques. La production est effectuée en France à Dunkerque (70 000 t/an de silicomanganèse), en Norvège à Porsgrunn (170 000 t/an), Sauda (220 000 t/an) et Kvinesdal (165 000 t/an), aux États Unis à Marietta (120 000 t/an) et depuis 2015, au Gabon à Moanda avec 65 000 t/an de silicomanganèse et 20 000 t/an de manganèse métal.
- Ferroglobe, après le rachat, en 2017, des activités de Glencore dans le ferromanganèse qui elle même avait acquis, en 2012, des activités européennes de Vale dans les alliages de manganèse, a vendu, en 2019, 392 456 t d’alliages de manganèse avec des capacités de 309 000 t/an de ferrosilicomanganèse et de 346 000 t/an de ferromanganèse à Grande-Synthe, près de Dunkerque, en France, Mo I Rana, en Norvège, Cee et Boo, en Espagne.
- South32 (ex BHP Billiton) : a produit, en 2019, 223 000 t d’alliages de manganèse dont 69 000 t en Afrique du Sud et 154 000 t en Australie. Exploite à 60 % (avec 40 % pour Anglo American) l’usine Metalloys à Meyerton en Afrique du Sud et l’usine TEMCO à Bell Bay, en Tasmanie (Australie).
- Anglo American, a produit, en 2019, en Australie et Afrique du Sud, 149 000 t d’alliages dans les sociétés communes avec South32.
- Compania Minera Autlan (Mexique) possède une capacité de production de 231 000 t/an d’alliages, dans 3 usines, Tamós, dans l’État de Veracruz, avec 144 000 t/an, Teziutlán, dans l’État de Puebla, avec 54 000 t/an et Gómez Palacio, dans l’État de Durango, avec 33 000 t/an. La production, en 2017, a été de 236 000 t d’alliages.
- Vale : production de 151 000 t d’alliages de manganèse, en 2019, dont 86 000 t à Simões Filho, dans l’État de Bahia, et 54 000 t à Barbacena et 11 000 t à Ouro Preto dans l’État de Minas Gerais.
- Manganese Metal Company (Afrique du Sud) produit du manganèse métal par voie électrolytique (MMC) à 99,9 % de pureté dans son usine de Nelspruit, avec une capacité de production est 30 000 tonnes par an.
Situation française
Production et commerce extérieur
Minerai
En 2019.
Pas de production minière, mais la société française Eramet, deuxième producteur mondial de minerai de manganèse avec sa filiale à 63,71 %, Comilog, exploite le gisement de Moanda au Gabon. La production est de 4,765 millions de tonnes de minerai.
- Exportations : 47 825 t vers l’Espagne à 75 %, l’Allemagne à 11 %, l’Italie à 5 %.
- Importations : 480 648 t du Gabon à 53 %, d’Afrique du Sud à 47 %.
Alliages de manganèse et manganèse
La France est un producteur de ferromanganèses et ferrosilicomanganèse.
Productions, en 2015 : 98 000 t de ferrosilicomanganèse et 146 000 t de ferromanganèse carburé.
Commerce extérieur
En 2019.
Ferrosilicomanganèse :
- Exportations : 49 700 t vers l’Allemagne à 81 %, le Royaume Uni à 14 %, la Belgique à 3 %.
- Importations : 47 050 t de Norvège à 33 %, d’Italie à 20 %, des Pays Bas à 18 %, de Géorgie à 7 %.
Ferromanganèse carburé :
- Exportations : confidentielles.
- Importations : 36 910 t de Norvège à 40 %, de Malaisie à 27 %, d’Espagne à 9 %.
Ferromanganèse affiné :
- Exportations : 381 t vers la Suède à 26 %, le Maroc à 13 %, l’Autriche à 12 %, la République tchèque à 8 %.
- Importations : 6 691 t d’Afrique du Sud à 68 %, des Pays Bas à 13 %, d’Allemagne à 5 %.
Manganèse :
- Exportations : 123 t vers l’Italie à 15 %, l’Allemagne à 12 %.
- Importations : 7 861 t de Chine à 72 %, d’Espagne à 12 %, des Pays Bas à 9 %.
Oxydes de manganèse :
- Exportations : 12 310 t vers le Danemark à 49 %, la Belgique à 26 %, l’Allemagne à 15 %.
- Importations : 12 110 t de Corée du Sud à 43 %, d’Afrique du Sud à 18 %, de Géorgie à 11 %.
Producteurs
Eramet :
- Extrait, avec sa filiale Comilog, du minerai au Gabon dans la mine de Moanda. C’est le 2ème producteur mondial de minerai de haute teneur avec, en 2019, une production de 4,765 millions de tonnes.
- Produit des alliages de manganèse : c’est le 2ème producteur mondial d’alliages de manganèse pour la sidérurgie, voir ci-dessus. La production française est réalisée à Dunkerque avec 70 000 t/an de ferrosilicomanganèse.
- Recycle, avec sa filiale Valdi, le dioxyde de manganèse de piles dans la fabrication de ferroalliages, en France, à Feurs (42).
Ferroglobe, après avoir acquis, en novembre 2017, les activités de Glencore dans le ferromanganèse, exploite à Grande-Synthe, près de Dunkerque, une usine de fabrication d’alliages de manganèse à l’aide du plus grand four de ferro-alliages de manganèse dans le monde d’une puissance de 102 MVA. Les capacités de production de ferroalliages de manganèse sont de 140 000 t/an.
Utilisations
Consommations
Sous forme de minerai : dans le monde, en 2013, 18,2 millions de tonnes de Mn contenu dans des minerais, soit le 4ème métal le plus utilisé après le fer, l’aluminium et le cuivre, devant le zinc. Par pays :
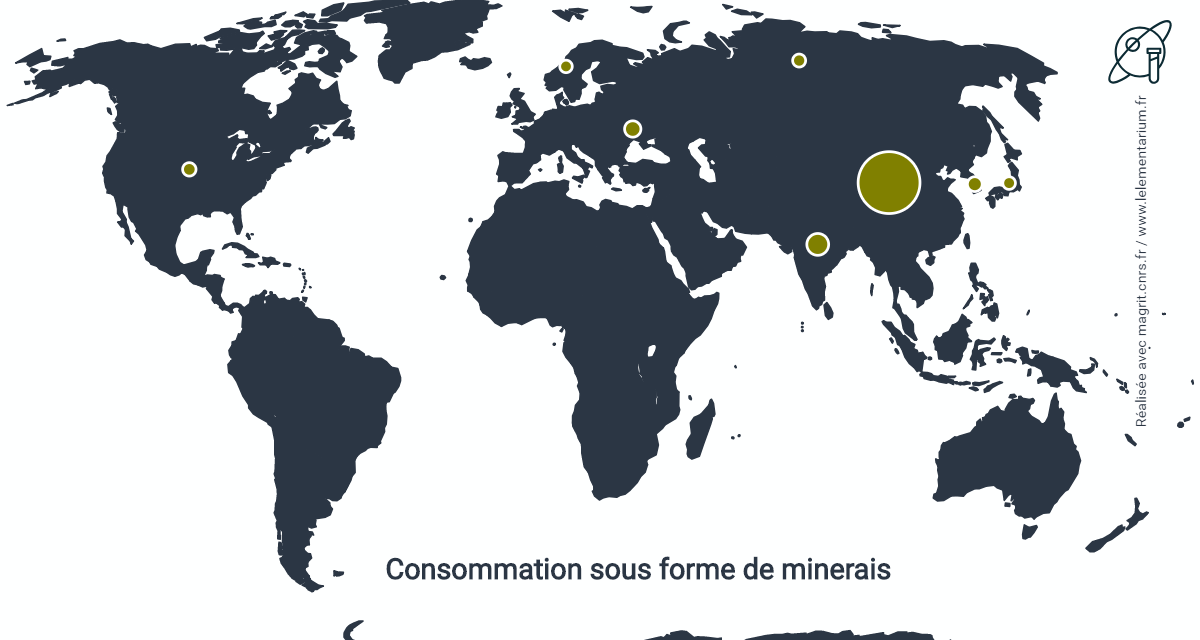
en milliers de tonnes
Chine |
10 830 |
|
États-Unis, en 2014 |
508 |
Inde |
1 346 |
|
Russie |
477 |
Ukraine |
753 |
|
Japon |
451 |
Corée du Sud |
619 |
|
Norvège |
442 |
Source : RPA, « Manganese, The Global Picture – A Socio Economic Assessment »En 2019, la consommation mondiale d’alliages est de 17,1 millions de t dont 18 millions de t de ferrosilicomanganèse, 4,5 millions de ferromanganèse carburé et 1,4 million de t de ferromanganèse affiné.
En 2012, la consommation de l’Union européenne, en Mn contenu dans les minerais, est de 462 200 t.
Sous forme d’alliages : en 2014, la consommation a été de 20,0 millions de t d’alliages dont 13,2 millions de t de ferrosilicomanganèse, 5,0 millions de t de ferromanganèse carburé et 1,9 million de t de ferromanganèse affiné. Par pays et type d’alliage, en 2013 :
en milliers de t de Mn contenu
|
Total |
Silicomanganèse |
Ferromanganèse carburé |
Ferromanganèse affiné |
Total |
19 314 |
13 262 |
4 265 |
1 687 |
Chine |
11 813 |
8 988 |
4 265 |
852 |
Inde |
1 151 |
794 |
304 |
53 |
Japon |
903 |
310 |
456 |
137 |
États-Unis, en 2014 |
411 |
96 |
294 |
20 de métal |
Source : RPA, « Manganese, The Global Picture – A Socio Economic Assessment »
En 2012, la consommation de l’Union européenne est de 1,488 million de t d’alliages dont 872 100 t de ferrosilicomanganèse, 442 600 t de ferromanganèse carburé et 173 400 t de ferromanganèse affiné.
Secteurs d’utilisation
En 2014.
Sidérurgie |
91 % |
|
Batteries et piles |
3 % |
Métaux non ferreux |
4 % |
|
|
|
Sidérurgie : le manganèse, introduit à l’étape du haut fourneau, est pour sa plus grande partie oxydé et ne se retrouve pas dans la fonte. Le manganèse doit être ajouté en aciérie, lors de l’affinage de la fonte. Il a longtemps joué un rôle essentiel de désoxydant (en complément du silicium) et de désulfurant. Ces rôles sont actuellement réduits (30 % des ajouts de Mn) au bénéfice de celui d’élément d’alliage (70 % des ajouts de Mn). Le manganèse abaisse la température de transformation de l’austénite en ferrite et permet ainsi d’éviter l’accumulation de cémentite aux joints de grains. Il joue aussi sur la structure de la perlite, en apportant de la dureté à l’acier. Ainsi, la présence de manganèse dans les gisements de fer exploités par Sparte dans la Grèce ancienne est l’une des causes de la supériorité de son armement.
La majeure partie des aciers contient de 0,15 à 0,8 % de Mn, soit une consommation moyenne de 6 à 7 kg/t d’acier. Le manganèse contenu dans l’acier final ne représente qu’environ 1/3 du manganèse consommé : les 2/3 du manganèse introduit sont perdus par oxydation et se retrouvent, principalement, dans les scories.
Les aciers inoxydables contiennent environ 1 % de Mn (dans certains cas jusqu’à 4 et même 16 %). Les aciers inoxydables de la série 200, contenant moins de nickel, sont de plus en plus employés en remplacement des aciers des séries 300 et 400. Leur teneur en manganèse est de 9 % au lieu d’environ 1 % pour ceux des séries 300 et 400.
Les aciers laminables à haute résistance mécanique contiennent de 1 à 1,8 % de Mn, pour fabriquer des oléoducs, des coques de navire… Les aciers à haute limite élastique, de 0,7 à 1,6 % de Mn. L’acier Hadfield, non magnétique et très résistant à l’abrasion, contient 12 à 14 % de Mn et 1,25 % de C : il est irremplaçable pour les aiguillages de voies ferrées.
L’allègement des véhicules automobiles est réalisé, en partie, en faisant appel à des aciers à « haute résistance » qui contiennent environ 0,9 % de Mn au lieu des 0,4 % des aciers traditionnels employés dans ce secteur d’application.
Autres utilisations
Dans les métallurgies non ferreuses, les piles, l’agriculture, les catalyseurs, les céramiques, la pharmacie…
Alliages d’aluminium : la présence de manganèse renforce leur résistance à la corrosion. Ces alliages sont employés, par exemple, dans la fabrication de boîtes-boisson. Ce sont les alliages de la série 3000 avec de 0,8 à 1,5 % de Mn.
Alliages de cuivre : Mn est utilisé pour désoxyder et améliorer leurs propriétés mécaniques et de moulage. L’alliage Cu : 84 %, Mn : 12 %, Ni : 4 % a une résistivité invariante en fonction de la température.
Piles et batteries : 3ème débouché important du manganèse (sous forme d’oxyde). Dans les piles salines ou alcalines, MnO2 est utilisé au pôle + en présence de carbone (graphite naturel ou noir d’acétylène) qui augmente la conductibilité électrique. Il joue un rôle de dépolarisant car, étant plus oxydant que H3O+, il évite la formation, par électrolyse, de H2 qui formerait autour de l’électrode + une couche isolante et ainsi polariserait et arrêterait la pile. Dans le cas des piles salines cylindriques, l’axe de la pile est constitué d’un crayon de graphite plongeant dans l’aggloméré MnO2-carbone. Le pôle -, en zinc, constitue le boîtier.
Le dioxyde de manganèse utilisé doit être actif électrochimiquement. Pour cela, il doit être constitué de MnO2 de structure alpha ou gamma, à des teneurs de 75-95 %, et contenir des ions Mn4+, Mn3+, des groupements acides et de l’eau. MnO2 actif peut être naturel (dioxyde NMD extrait au Gabon, au Ghana, au Brésil, en Chine, au Mexique, en Inde) ou artificiel (obtenu par synthèse chimique (dioxyde CMD) ou électrolytique (dioxyde EMD destiné aux piles alcalines)). Le dioxyde naturel le plus courant est la pyrolusite (structure bêta) qui n’est pas active mais peut être rendue active (dioxyde AMD).
En France, la consommation d’énergie provenant de piles est de 2 à 3.106 kWh (les centrales électriques thermiques et hydrauliques fournissent près de 5.1011 kWh).
Les capacité mondiales de production d’oxyde EMD sont, en 2019, de 604 000 t/an avec, par pays, en 2015 :
en t/an
Chine, en 2019 |
452 000 t/an |
|
Espagne |
11 000 t/an |
États-Unis |
70 500 t/an |
|
Colombie |
6 000 t/an |
Japon |
33 000 t/an |
|
Inde |
1 000 t/an |
Grèce |
26 000 t/an |
|
|
|
Source : Li Tongqing, 6th International Forum of Mn Electrolytic Products, mars 2016, Nanning, China
En 2019, la production est de 455 228 t dont 373 500 t en Chine.
Pour l’ensemble des types d’oxydes, le commerce international a porté, en 2019, sur 305 571 t.
Les exportations de la Chine sont de 58 881 t, celle de l’Afrique du Sud de 49 090 t, de l’Inde de 22 598 t.
Les principaux pays importateurs sont la Belgique avec 22 739 t, les États-Unis avec 21 969 t, l’Inde avec 20 467 t, l’Indonésie avec 21 000 t, l’Allemagne avec 17 422 t.
L’oxyde EMD est utilisé, en 2019, à 63 % dans des piles alcalines, 20 % dans des piles salines, et 17 % dans des batteries lithium oxyde de manganèse (LMO).
Agriculture : dans ce secteur, où il est indispensable en particulier à la photosynthèse, le manganèse est employé sous forme de sulfate MnSO4. La production mondiale, en 2019, de ce dernier, est de 541 500 t dont 373 500 t en Chine et 90 000 t en Inde, pour une capacité de production mondiale de 890 000 t/an par 33 producteurs dont 21 en Chine et 5 en Inde. Il est destiné à 83 % à l’agriculture et à 17 % à un emploi dans des piles.
Fongicide sous forme de manganèse-éthylène bisdithiocarbamate (Mn-EBDC), élément actif principal du maneb, 200 000 tonnes de maneb sont consommées par an dans le monde.
Élaboration du permanganate de potassium : le procédé électrochimique a supplanté le procédé chimique (oxydation du manganate par le dichlore).
1ère étape : oxydation de la pyrolusite, par le dioxygène de l’air, en présence d’hydroxyde de potassium :
MnO2 + 1/2 O2 + 2 OH– = MnO42- + H2O
2ème étape : électrolyse de la solution de manganate (200 g/L), en présence de KOH, à 60°C. Les ions MnO42- sont oxydés, à l’anode, en ions MnO4–. Les anodes sont en acier recouvert de Ni. Les cathodes, en acier, sont gaînées d’un revêtement poreux (en PVC, par exemple). La consommation est de 0,8 à 0,9 kWh/kg. Le permanganate est obtenu par cristallisation après refroidissement de la solution. La production mondiale est d’environ 40 000 t/an, la Chine étant un important exportateur.
Le permanganate de potassium est un oxydant puisant, un bactéricide et un algicide. Il est utilisé dans la purification de l’eau potable, le traitement des eaux usées, la désodorisation des rejets d’usines (peinture, conditionnement du poisson…).
Bibliographie
- International Manganese Institute (IMnI), 56 rue de Londres, 75008 Paris.
- RPA, « Manganese, The Global Picture A Socio Economic Assessment », report for the International Manganese Institute, Loddon, Norfolk, UK, 2015.
- A. d’Harambure, « Overview of the global manganese industry« , IMnI, Metal Bulletin Conférence, Singapour, mars 2016.
M. Giblin, « Manganese minig outlock, improves, but for how long ? », S&P Global, août 2017.
- L’Actualité Chimique, janvier, février 1992.
- Rapport d’activité d’Eramet, 33 av du Maine, 75755 Paris Cedex 15.
Commentaires récents