Données physico-chimiques
Données atomiques
Numéro atomique |
Masse atomique |
Configuration électronique |
Structure cristalline |
Rayon métallique pour la coordinence 12 |
82 |
207,2 g.mol-1 |
[Xe] 4f14 5d10 6s2 6p2 |
cubique à faces centrées de paramètre a = 0,4950 nm |
175,0 pm |
Données physiques
Masse volumique |
Dureté |
Température de fusion |
Température d’ébullition |
Conductibilité électrique |
Conductibilité thermique |
Solubilité dans l’eau |
11,343 g.cm-3 |
1,5 |
327,50°C |
1 740°C |
4,81.106 S.m-1 |
35,3 W.m-1.K-1 |
insoluble |
Données chimiques
Électronégativité de Pauling |
pKa : Pb2+aq/PbOH+aq |
pKs : PbCO3 |
pKs : Pb(OH)2 |
pKs : Pb(OH)4 |
pKs : PbS
|
pKs : PbSO4 |
pKs : PbF2 |
pKs : PbCl2 |
pKs : PbBr2 |
pKs : PbI2 |
pKs : PbCrO4 |
2,33 |
8 |
10,8 |
14,5 |
64 |
28 |
42,1 |
7,6 |
4,7 |
4,4 |
8,1 |
12,5 |
Potentiels standards :
PbO(s) + H2O + 2e = Pb(s) + 2OH– |
E° = -0,58 V |
PbO2(s) + H2O + 2e = PbO(s) + 2OH– |
E° = 0,28 V |
3PbO2(s) + 2H2O + 4e = Pb3O4(s) + 4OH– |
E° = 0,29 V |
Pb3O4(s) + H2O + 2e = 3PbO(s) + 2OH– |
E° = 0,25 V |
PbO2(s) + 4H+ + 2e = Pb2+ + 2H2O |
E° = 1,45 V |
PbO(s) + 2H+ + 2e = Pb(s) + H2O |
E° = 0,25 V |
Pb4+ + 2e = Pb2+ |
E° = 1,8 V |
Pb2+ + 2e = Pb(s) |
E° = -0,126 V |
Données thermodynamiques
Plomb cristallisé :
- Entropie molaire standard à 298,15 K : S° = 64,8 J.K-1mol-1
- Capacité thermique molaire sous pression constante à 298,15 K : Cp° = 26,4 J.K-1mol-1
- Enthalpie molaire standard de fusion à la température de fusion : 5,1 kJ.mol-1
- Enthalpie molaire standard d’ébullition à la température d’ébullition : 180 kJ.mol-1
|
Plomb gazeux :
- Enthalpie molaire standard de formation à 298,15 K : 195 kJ.mol-1
- Enthalpie libre molaire standard de formation à 298,15 K : 162 kJ.mol-1
- Entropie molaire standard à 298,15 K : S° = 175,3 J.K-1mol-1
- Capacité thermique molaire sous pression constante à 298,15 K : Cp° = 20,8 J.K-1mol-1
|
Données industrielles
Matières premières
La teneur moyenne en plomb de l’écorce terrestre est de 16 ppm.
Dans les minerais, le plomb est très souvent associé au zinc mais aussi à de nombreux autres éléments : Fe, Cu, Cd, Bi, Sb, Ge, As, Ag, Au, … qui sont en grande partie (sauf Fe) récupérés lors des opérations métallurgiques. Par exemple, en 2018, 38 % de la production mondiale d’argent provient de mines de plomb-zinc. En moyenne, pour 1 t de plomb, la production minière donne également 2 t de zinc et 3 kg d’argent.
Les revenus de la raffinerie de Trail, au Canada, du groupe Teck qui traite une partie du minerai de la mine de zinc-plomb de Red Dog, en Alaska, provenaient, en 2011, à 46 % de la production d’argent, 39 % de zinc, 12 % de plomb, 2,7 % d’indium, 1,84 % de germanium, 0,18 % de cadmium.
Les minerais mixtes Pb-Zn représentent 70 % de la production minière de plomb, les minerais de plomb, 20 % et 10 % de la production de plomb provient d’une coproduction lors du traitement de minerais de cuivre, zinc ou d’autres métaux.
En 2010, environ 240 mines étaient exploitées dans le monde.
La production minière mondiale ne représente, en 2019, que 40,1 % de la consommation totale, le recyclage du plomb étant particulièrement bien développé. La part de la production primaire était de 53 %, en 1999.
Minerais : le principal est la galène (PbS) très souvent associée à la blende et à la pyrite.
Les autres minerais exploités sont la cérusite (PbCO3) et l’anglésite (PbSO4) provenant de l’oxydation de PbS, présents dans les parties supérieures des gisements de galène.
La teneur des minerais tout venant est comprise entre 1 et 12 % de Pb.
Minéralurgie : elle est effectuée sur les lieux d’extraction, dans des laveries. La concentration a lieu par gravimétrie après broyage grossier ou par flottation après broyage plus fin. On obtient des concentrés de teneurs comprises entre 60 et 80 % de plomb, sous forme de PbS. Voir un exemple de flottation dans le chapitre zinc.
Productions minières
En 2019. Monde : 4,706 millions de t de Pb contenu, Union européenne, en 2017 : 207 000 t, en Pologne, Suède, Bulgarie, Irlande, Grèce.
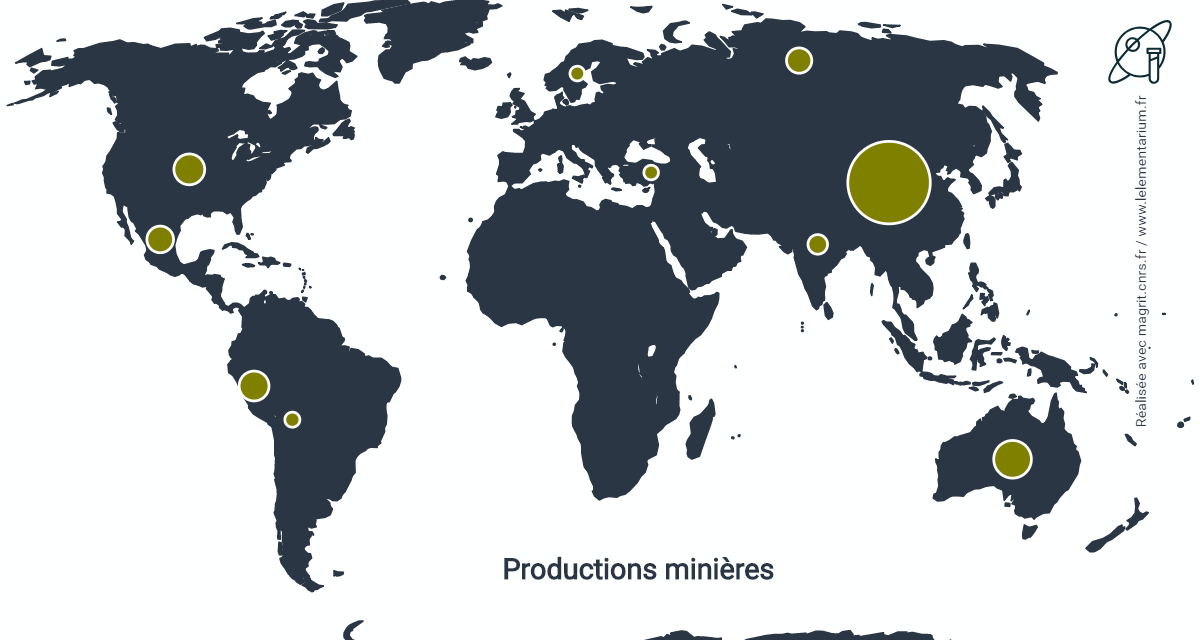
en milliers de t de Pb contenu
Chine |
2 058 |
|
Russie |
220 |
Australie |
474 |
|
Inde |
201 |
Pérou |
308 |
|
Bolivie |
100 |
États-Unis |
283 |
|
Kazakhstan |
90 |
Mexique |
261 |
|
Turquie |
70 |
En Australie :
- South32 (issue en mai 2015 de BHPBilliton) exploite souterrainement la mine de Cannington, dans le nord-ouest du Queensland, avec une production, en 2019, dans les concentrés miniers, de 101 400 t de Pb, 51 600 t de zinc, 379 t d’argent et des réserves prouvées et probables de 23 millions de t de minerai contenant 5,46 % de Pb, 3,40 % de Zn et 183 g/t de Ag. En 2019, 2,495 millions de t de minerai ont été traitées avec une teneur de 5,0 % de Pb, 3,0 % de Zn, 184 g/t de Ag.
- Glencore exploite, en 2019, les mines de :
- Mount Isa, au nord-ouest du Queensland, avec une production dans les concentrés miniers de 326 400 t de Zn, 158 000 t de Pb et 172 t de Ag et des réserves prouvées et probables d’un total de 79 millions de t contenant 7,4 % de Zn, 3,6 % de Pb et 66 g/t de Ag.
- McArthur River, au nord-est du Territoire du Nord, avec une production dans les concentrés miniers de 271 200 t de zinc, 55 300 t de plomb et 52 t d’argent et des réserves prouvées et probables de 98 millions de t renfermant 9,1 % de Zn, 4,2 % de Pb et 42 g/t d’Ag.
- MMG, détenu à 74 % par China Minmetals Corporation, exploite, en 2019, les mines de :
- Rosebery, en Tasmanie, avec une production dans les concentrés miniers de 75 721 t de Zn, 28 744 t de Pb, 1 465 t de Cu, 91 t de Ag et 1,1 t d’or et des réserves prouvées et probables de 5,4 millions de t renfermant 8,0 % de Zn, 3,0 % de Pb, 0,21 % de Cu, 114 g/t de Ag et 1,4 g/t d’or.
- Dugald River, dans le Queensland, avec contenu dans des concentrés, 147 320 t de Zn, 16 693 t de Pb et 27,8 t de Ag. Les réserves prouvées et probables sont de 28,6 millions de t renfermant 11,7 % de Zn, 2,0 % de Pb, 38 g/t de Ag.
- LeadFX, société canadienne, exploite la mine à ciel ouvert de carbonate de plomb de Paroo Station (ex mine Magellan), située en Australie Occidentale. Pendant quelques années, les autorités australiennes ont interrompu le transport des concentrés jusqu’aux installations portuaires d’exportation, ce qui a entraîné l’arrêt de l’exploitation, jusqu’à ce qu’une solution soit trouvée à l’émission de poussières riches en plomb émises lors du transport. Les conditions de transport adoptées ont été les suivantes :
- Les concentrés sont placés dans des sacs hydrofuges de 2 t, nettoyés extérieurement par aspiration.
- Les sacs sont placés ensuite dans des conteneurs lavés extérieurement sous pression, l’air de conteneurs témoins étant contrôlé ainsi que l’ensemble des opérations par un inspecteur indépendant.
Le transport des concentrés a repris mi-2013, avec une production, en 2014, de 80 900 t de plomb contenu dans les concentrés. Les réserves prouvées et probables sont de 36,3 millions de t de minerai renfermant 3,7 % de plomb. Début 2015, la production a été de nouveau arrêtée. La production pourrait reprendre avec la construction d’une usine de traitement hydrométallurgique du minerai et une capacité de production de 70 000 t/an de lingots de plomb.
Au Pérou :
- Volcan a produit, en 2019, 239 000 t de Zn, 49 400 t de Pb, 4 500 t de Cu, 485 t de Ag et 672 kg de Au. Exploite 4 complexes miniers :
- Yauli avec 4 mines souterraines et l’extraction de 3,170 millions de t de minerai renfermant 141 000 t de Zn, 20 000 t de Pb, 3 000 t de Cu et 218 t de Ag.
- Changar avec 2 mines souterraines et l’extraction de 1,7 million de t de minerai renfermant 74 700 t de Zn, 18 400 t de Pb, 2 000 t de Cu et 100 t de Ag.
- Alpamarca avec une mine souterraine et une à ciel ouvert et l’extraction de 950 000 t de minerai renfermant 5 920 t de Zn, 4 660 t de Pb, 400 t de Cu et 37,6 t de Ag.
- Cerro de Pasco avec 2 mines souterraines et une à ciel ouvert et l’extraction de 2,1 millions de t de minerai renfermant 17 500 t de Zn, 6 300 t de Pb et 24,6 t de Ag.
- Par ailleurs le traitement par lixiviation de 911 000 t de terrils a donné 103 t de Ag et 479 kg de Au.
Les réserves prouvées et probables sont, fin 2019, de 32,7 millions de t de minerai renfermant 4,8 % de Zn, 1,1 % de Pb, 0,17 % de Cu et 93 g/t de Ag. En 2017, le groupe Glencore a acquis 55,03 % des actions de classe A de la société Volcan.
- Milpo, devenu, en 2017, Nexa Resources Perú, est détenue à 80,06 % par Nexa Resources, ex-Votorantim. La société exploite, en souterrain, 3 mines : El Porvenir, Cerro Lindo et à 62,03 % Atacocha. En 2019, la production a été de 197 647 t de zinc, 45 611 t de plomb, 38 184 t de cuivre, 266 t d’argent et 773 kg d’or. Les revenus de la société proviennent, en 2017, à 48 % des ventes de zinc, 27 % de celles de cuivre, 12 % d’argent, 9 % de plomb et 4 % d’or.
- En 2019, la mine de Porvenir a produit 54 689 t de zinc, 16 891 t de plomb, 465 t de cuivre, 106 t d’argent et 301 kg d’or contenu dans les concentrés. Les réserves prouvées et probables sont de 16,2 millions de t de minerai renfermant 3,70 % de Zn, 0,75 % de Pb, 0,23 % de Cu et 46,9 g/t de Ag.
- La mine de Cerro Lindo a produit 126 290 t de zinc, 12 257 t de plomb, 37 677 t de cuivre, 101 t d’argent et 128 kg d’or contenu dans les concentrés. Les réserves prouvées et probables sont de 48,4 millions de t de minerai renfermant 1,26 % de Zn, 0,16 % de Pb, 0,65 % de Cu et 18,4 g/t de Ag.
- La mine d’Atacocha a produit 16 668 t de zinc, 14 465 t de plomb, 41 t de cuivre, 58,5 t d’argent et 431 kg d’or contenu dans les concentrés. Les réserves prouvées et probables sont de 3,9 millions de t de minerai renfermant 3,77 % de Zn, 1,73 % de Pb, 0,23 % de Cu et 78,8 g/t de Ag auxquelles s’ajoutent 5,3 millions de t renfermant 1,10 % de Zn, 0,86 % de Pb, 0,03 % de Cu, 29,8 g/t de Ag, 0,25 g/t de Au.
- La Sociedad Minera Corona, détenue à 81,84 % par Sierra Metals, qui exploite la mine souterraine de Yauricocha, a extrait, en 2019, 1,117 million de t de minerai contenant 81 083 t de zinc, 34 548 t de plomb, 20 059 t de cuivre, 56 t d’argent et 130 kg d’or. Les teneurs du minerai extrait sont de 3,72 % de Zn avec un taux de récupération de 88,5 %, de 1,57 % de Pb avec un taux de récupération de 89,3 %, de 1,06 % de Cu avec un taux de récupération de 77,1 %, de 63 g/t d’argent avec un taux de récupération de 79,2 %, de 0,59 g/t d’or avec un taux de récupération de 19,7 %. Les réserves prouvées et probables sont de 8,44 millions de t de minerai renfermant 3,07 % de Zn, 0,78 % de Pb, 1,13 % de Cu, 46,5 g/t de Ag et 0,50 g/t de Au.
- El Brocal, détenue à 61,43 % par Buenaventura, exploite à ciel ouvert la mine de plomb-zinc de Tajo Norte et celle souterraine de cuivre de Marcapunta Norte. En 2019, l’extraction de 6,3 millions de t de minerai renfermait 43 580 t de zinc, 43 394 t de cuivre, 23 599 t de plomb, 136 t d’argent et 582 kg d’or. Les réserves prouvées et probables de Tajo Norte sont de 14,8 millions de t de minerai renfermant 2,52 % de zinc, 1,17 % de plomb, 1,71 % de cuivre et 33,6 g/t d’argent.
- Los Quenuales, détenue à 97,6 % par Glencore avec 3 mines : Iscaycruz, qui a produit en 2019, 410 000 de minerai renfermant 5,3 % de Zn, 0,7 % de Pb, 0,4 % de Cu et 43 g/t de Ag avec des réserves prouvées et probables de 2,2 millions de t renfermant 5,8 % de Zn, 0,7 % de Pb, 0,2 % de Cu et 45 g/t de Ag, Yauliyacu qui a produit, en 2019, 1,3 million de t de minerai renfermant 2,0 % de Zn, 0,7 % de Pb et 72 g/ d’argent avec des réserves prouvées et probables de 9 millions de t renfermant 2,1 % de Zn, 0,9 % de Pb, 0,2 % de Cu et 118 g/t de Ag et Contonga qui a produit, en 2019, 0,156 million de t de minerai renfermant 2,3 % de Zn, 0,4 % de Pb, 0,8 % de Cu et 42 g/t de Ag avec des réserves prouvées et probables de 1,2 million de t de minerai renfermant 3,4 % de Zn, 1,1 % de Pb, 0,6 % de Cu et 61 g/t de Ag.
Aux États-Unis, en 2019, 11 mines sont en activité, 6 mines de plomb dans le Missouri et 5 mines où le plomb est co-produit, deux en Alaska (mines à ciel ouvert de Red Dog et souterraine de Greens Creek), deux dans l’Idaho (mines Lucky Friday et Galena) et une dans l’État de Washington (mine souterraine de Pend Oreille). En 2000, 19 mines étaient exploitées, avec une production de 465 000 t de plomb contenu.
- Doe Run, filiale du groupe Renco, exploite les mines du Missouri (mines souterraines de Buick, Casteel, Fletcher, Brushy Creek, n°29 et Sweetwater).
- Teck exploite les mines plomb-zinc de Red Dog et Pend Oreille. La mine de Red Dog, en Alaska, a produit, en 2019, dans les concentrés miniers, 552 400 t de zinc et 102 800 t de plomb, voir le chapitre zinc. Les réserves prouvées et probables sont de 50,9 millions de t de minerai renfermant 12,9 % de zinc, 3,6 % de plomb et 67,7 g/t d’argent.
La mine de Pend Oreille, dans l’État de Washington, dont l’exploitation souterraine, a redémarré en décembre 2014, a produit, en 2019, 19 400 t de zinc dans des concentrés miniers. La production a été suspendue fin juillet 2019.
- Hecla Mining exploite les mines d’argent de Greens Creek, en Alaska, avec, en 2019, une production de 56 805 t de zinc, 20 112 t de plomb, 308 t d’argent, 1,8 t d’or et des réserves prouvées et probables de 10,7 millions de t de minerai renfermant 7,3 % de Zn, 2,8 % de Pb, 379 g/t de Ag et 2,8 g/t de Au et Lucky Friday, dans l’Idaho, avec, en 2019, une production de 4 098 t de plomb, 2 052 t de zinc, 20 t d’argent et des réserves prouvées et probables de 5,6 millions de t de minerai renfermant 4,0 % de Zn, 9,1 % de Pb et 448 g/t de Ag.
- La mine d’argent de Galena, exploitée à 60 % par Americas Silver Corporation, a produit, en 2019, 5 614 t de plomb et 23 t d’argent et possède des réserves prouvées et probables de 479 000 t renfermant 7,02 % de Pb et 248 g/t de Ag.
Principaux producteurs : en 2019.
Sources : rapports des sociétés et Volcan
- Glencore exploite des mines :
- Au Kazakhstan au travers de 69,7 % de Kazzinc, avec, en 2019, une production de 172 500 t de zinc, 34 400 t de plomb, 44 000 t de cuivre, 144 t d’argent et 20 t d’or et des réserves prouvées et probables de 91 millions de t renfermant 3,6 % de Zn, 0,9 % de Pb, 0,2 % de Cu, 15 g/t de Ag et 0,7 g/t de Au.
- En Australie, dans le Queensland, à Mount Isa avec une production, en 2019, de 326 400 t de Zn, 158 000 t de Pb et 172 t de Ag et des réserves prouvées et probables d’un total de 79 millions de t contenant 7,4 % de Zn, 3,6 % de Pb et 66 g/t de Ag et dans le Territoire du Nord à Mc Arthur River avec 271 200 t de zinc, 55 300 t de plomb et 52 t d’argent et des réserves prouvées et probables de 98 millions de t renfermant 9,1 % de Zn, 4,2 % de Pb et 42 g/t d’Ag.
- Au Pérou à Iscaycruz, Yauliyacu et Contonga avec 97,6 % de parts.
- En Bolivie à Sinchi Wayra avec les mines de Bolivar et Porco et Illapa, avec 45 % de parts, et les mines de Poopo et Caballo Blanco.
- En Argentine, à Aguilar.
Au total, au Pérou, en Bolivie, en Argentine, la production dans des concentrés a été, en 2019, de 93 600 t de zinc, 32 300 t de plomb, 2 700 t de cuivre et 215 t d’argent et les réserves prouvées et probables de Glencore dans ces pays sont de 16,6 millions de t renfermant 4,3 % de Zn, 1,2 % de Pb, 0,2 % de Cu, 126 g/t de Ag.
En 2017, Glencore a pris une participation dans la société péruvienne Volcan lui assurant 65 % des votes.
- Hindustan Zinc (Inde), détenu à 64,9 % par le groupe Vedanta exploite 5 mines souterraines dans le Rajasthan avec une production, en 2019, de 728 498 t de zinc, 207 190 t de plomb et de 679 t d’argent contenu dans les concentrés :
- Rampucha Agucha, qui a produit, en 2019, 358 000 t de Zn, 35 600 t de Pb avec des réserves de 35,3 millions de t minerai renfermant 13,6 % de Zn, 1,8 % de Pb et 63 g/t de Ag.
- Sindesar Khurd, qui a produit 174 000 t de Zn, 108 000 t de Pb, avec des réserves de 32,5 millions de t de minerai renfermant 4,1 % de Zn, 3,2 % de Pb et 171 g/t de Ag.
- Zawar, avec 4 mines, a produit 55 000 t de Zn, 45 000 t de Pb avec des réserves de 10,1 millions de t de minerai renfermant 3,4 % de Zn, 1,8 % de Pb et 31 g/t de Ag.
- Rajpura Dariba, qui a produit 44 000 t de Zn, 9 000 t de Pb avec des réserves de 10,2 millions de t de minerai renfermant 5,1 % de Zn, 1,8 % de Pb et 51 g/t de Ag.
- Kayad, qui a produit 98 000 t de Zn, 10 000 t de Pb avec des réserves de 4,5 millions de t de minerai renfermant 5,4 % de Zn, 0,9 % de Pb et 18 g/t de Ag.
- Industrias Peñoles, au Mexique, avec une production, en 2019, de 292 291 t de zinc, 84 332 t de plomb, 31 294 t de cuivre, 1 939 t d’argent, 28,3 t d’or, exploite les mines suivantes :
- Velardeña, dans l’État de Durango, avec, en 2019, une production de 82 482 t de Zn, 5 257 t de Pb, 2 492 t de Cu, 27 t de Ag, 154 kg de Au et des réserves prouvées et probables de 50,2 millions de t de minerai renfermant 3,99 % de Zn, 0,28 % de Pb, 0,15 % de Cu, 15,8 g/t de Ag, 0,11 g/t de Au.
- Tizapa, dans l’État de Mexico, détenue à 51 %, avec 38 138 t de Zn, 8 197 t de Pb, 1 286 t de Cu, 180 t de Ag, 1,1 t de Au et des réserves de 9,7 millions de t de minerai renfermant 5,18 % de Zn, 1,23 % de Pb, 0,31 % de Cu, 207 g/t de Ag, 1,41 g/t de Au.
- Francisco Madero, dans l’État de Zacatecas, avec 41 451 t de Zn, 8 905 t de Pb, 895 t de Cu, 23 t de Ag et des réserves de 26,5 millions de t de minerai renfermant 2,02 % de Zn, 0,68 % de Pb, 0,07 % de Cu, 18,6 g/t de Ag.
- Sabinas, dans l’État de Zacatecas, avec 12 801 t de Zn, 4 936 t de Pb, 3 666 t de Cu, 88,6 t de Ag et des réserves de 33,8 millions de t de minerai renfermant 1,60 % de Zn, 0,87 % de Pb, 0,25 % de Cu, 82,1 g/t de Ag.
- Bismark, dans l’État de Chihuahua, avec 24 751 t de Zn, 1 315 t de Pb, 460 t de Cu, 9 t de Ag et des réserves de 1,24 million de t de minerai renfermant 5,00 % de Zn, 0,23 % de Pb, 0,30 % de Cu, 19 g/t de Ag.
Par ailleurs, Industrias Peñoles possède 75 % de la société Fresnillo qui, avec en 2019, une production de 92 578 t de zinc, 55 722 t de plomb, 1 699 t d’argent et 27,2 t d’or, exploite les mines suivantes :
-
- Fresnillo, dans l’État de Zacatecas, avec, en 2019, une production de 31 530 t de Zn, 21 472 t de Pb, 405 t de Ag, 1,6 t de Au et des réserves prouvées et probables de 22,6 millions de t renfermant 3,35 % de Zn, 1,57 % de Pb, 243 g/t de Ag, 0,78 g/t de Au.
- Saucito, dans l’État de Zacatecas, avec 29 506 t de Zn, 20 764 t de Pb, 534 t de Ag, 2,5 t de Au et des réserves de 14,9 millions de t de minerai renfermant 2,24 % de Zn, 1,29 % de Pb, 272 g/t de Ag, 1,42 g/t de Au.
- Ciénega, dans l’État de Durango, avec 8 986 t de Zn, 5 839 t de Pb, 180 t de Ag, 2,0 t de Au et des réserves de 8,9 millions de t de minerai renfermant 1,25 % de Zn, 0,82 % de Pb, 198 g/t de Ag, 2,08 g/t de Au.
- San Julián, dans l’État de Chihuahua, avec 22 697 t de Zn, 7 648 t de Pb, 675 t de Ag, 2,8 t de Au et des réserves de 14,0 millions de t de minerai renfermant 1,51 % de Zn, 0,59 % de Pb, 209 g/t de Ag, 0,12 g/t de Au.
- Boliden, avec une production, en 2019, de 290 000 t de zinc, 55 000 t de plomb, 372 t d’argent, 7,3 t d’or, exploite des mines en Suède et en Irlande. En Suède, les mines de Renström, Kristineberg, Maurliden, ont produit, en 2019, 58 000 t de zinc, 3 000 t de plomb, 4 000 t de cuivre, 75 t d’argent, 2,8 t d’or avec des réserves prouvées et probables de 7,6 millions de t renfermant 5,6 % de Zn, 0,7 % de Pb, 0,5 % de Cu, 162 g/t de Te, 74 g/t de Ag, 3,4 g/t de Au, ainsi que la mine de Garpenberg avec, en 2019, 109 000 t de zinc, 36 000 t de plomb, 700 t de cuivre, 257 t d’argent et 514 kg d’or et des réserves prouvées et probables de 74,9 millions de t renfermant 3,1 % de Zn, 1,4 % de Pb, 0,05 % de Cu, 96 g/t de Ag et 0,3 g/t de Au.
En Irlande exploite la mine de Tara, avec, en 2019, la production de 122 000 t de zinc, 16 000 t de plomb et 1,6 t d’argent et des réserves prouvées et probables de 17,4 millions de t renfermant 6,0 % de Zn et 1,6 % de Pb.
Commerce international : en 2019, pour les concentrés miniers.
Exportations des principaux pays sur un total mondial de 3,366 millions de t.
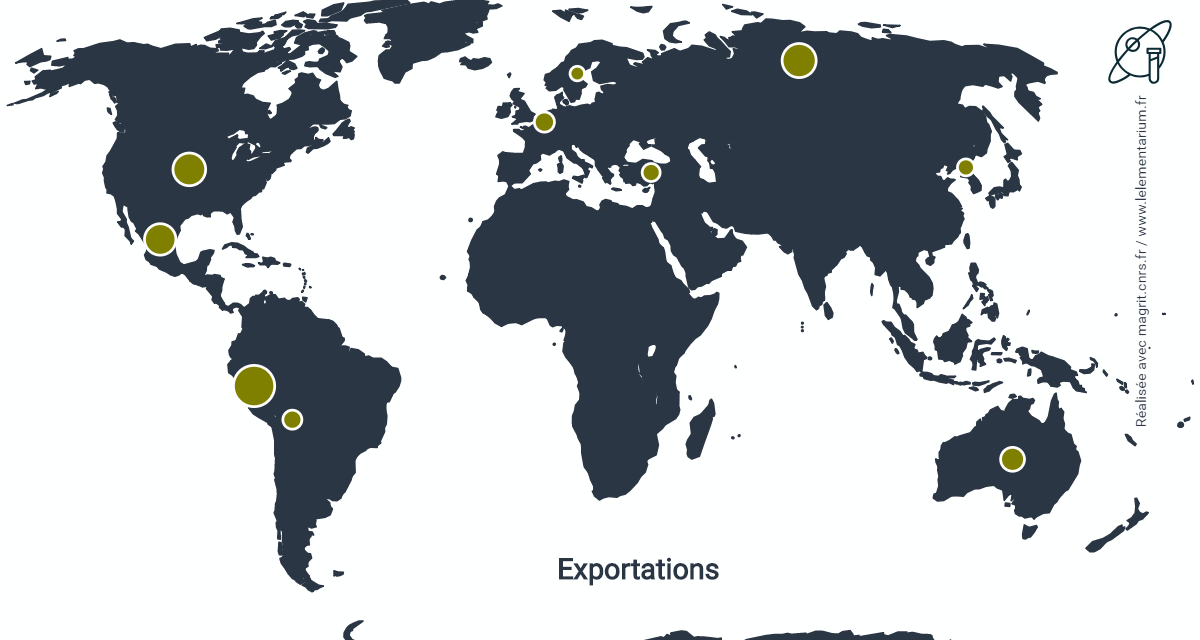
en milliers de t de concentrés miniers
Pérou |
470 |
|
Espagne |
206 |
Russie |
418 |
|
Mexique |
148 |
Australie |
414 |
|
Bolivie |
123 |
États-Unis |
285 |
|
Turquie |
119 |
Pays Bas |
215 |
|
Tadjikistan |
97 |
Les exportations du Pérou ont été dirigées à 44 % vers la Chine, 32 % vers la Corée du Sud, 8 % le Canada…
Importations des principaux pays sur un total mondial de 3,317 millions de t.
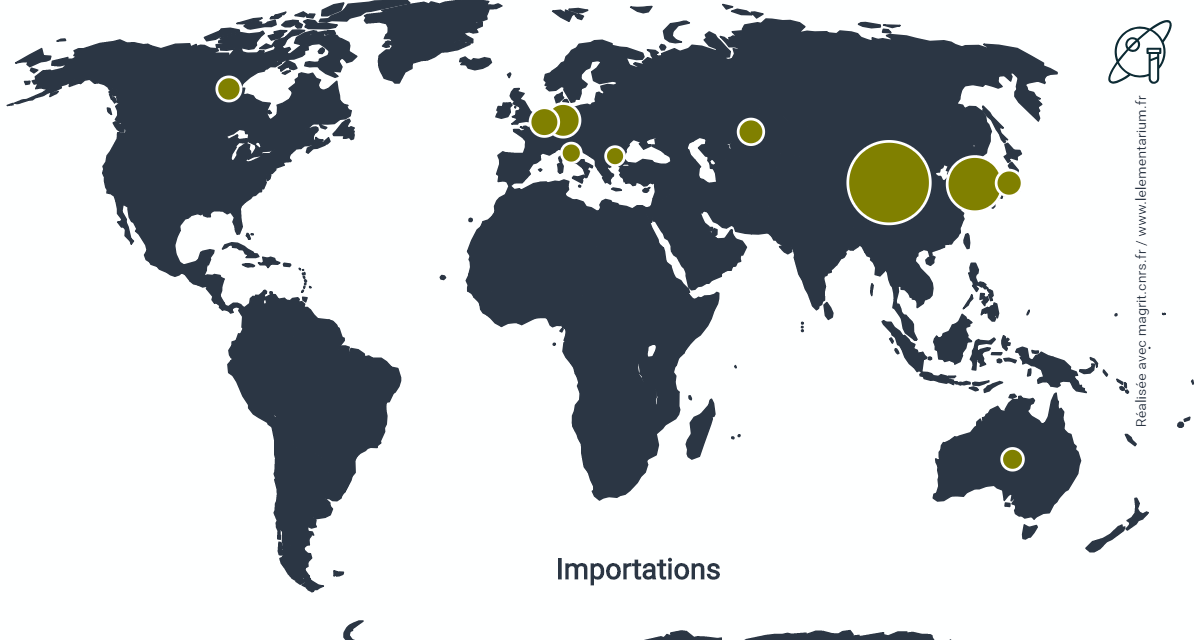
en milliers de t de concentrés miniers
Chine |
1 675 |
|
Pays Bas |
122 |
Corée du Sud |
580 |
|
Canada |
113 |
Allemagne |
186 |
|
Italie |
103 |
Kazakhstan |
146 |
|
Espagne |
70 |
Japon |
132 |
|
Bulgarie |
70 |
La Chine malgré sa production très importante a importé, en 2019, 1,675 million de t de concentrés de plomb provenant à 18 % de Russie, 13 % d’Australie, 10 % du Pérou, 8 % de Birmanie…
Réserves mondiales : en 2019. Monde : 90 millions de t de Pb contenu.
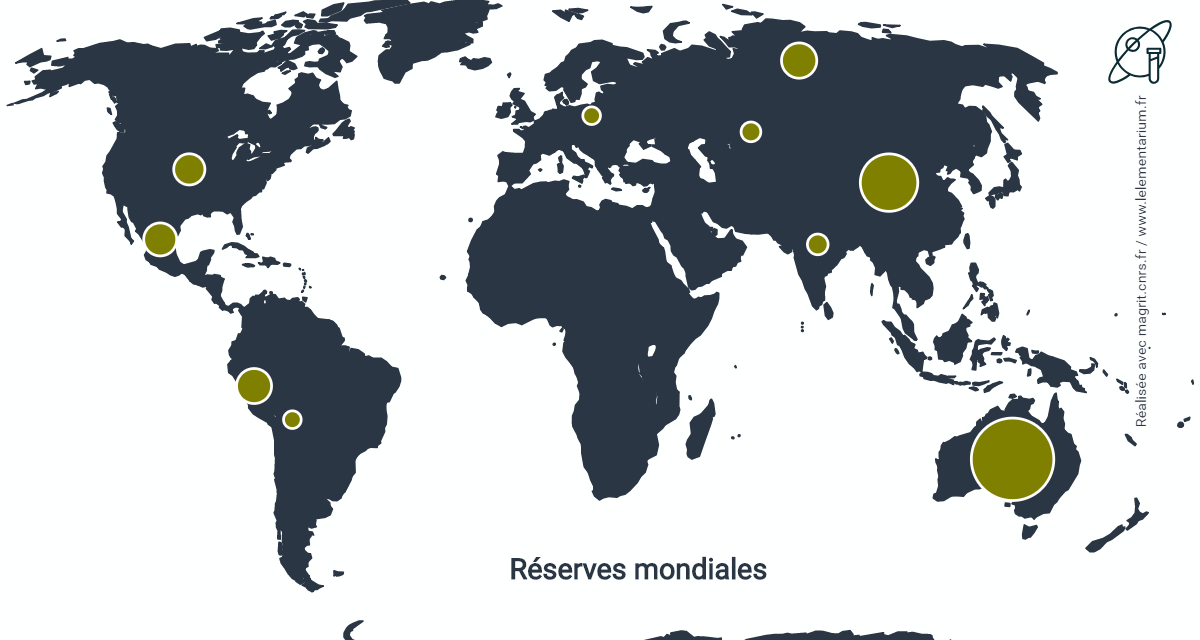
en milliers de tonnes de Pb contenu
Australie |
36 000 |
|
États-Unis |
5 000 |
Chine |
18 000 |
|
Inde |
2 500 |
Russie |
6 400 |
|
Kazakhstan |
2 000 |
Pérou |
6 300 |
|
Bolivie |
1 600 |
Mexique |
5 600 |
|
Pologne |
1 600 |
Situation française :
Il n’y a plus de production minière après la fermeture, en décembre 1991, de la mine des Malines (30), exploitée par la société Metaleurop. La production française avait atteint 30 000 t, en 1970.
En 2019, les importations sont de 25 t de concentrés en provenance à 60 % du Maroc et 40 % du Nigéria.
Métallurgie de première fusion
Traditionnellement cette métallurgie était réalisée en 2 étapes (grillage puis réduction), mais de nouveaux procédés pyrométallurgiques, en une étape, (KIVCET, Q.S.L, Isasmelt, …) sont de plus en plus utilisés.
Procédés en deux étapes
Grillage : il consiste à éliminer le soufre et à agglomérer le concentré afin qu’il résiste à l’écrasement lors de la réduction. La charge obtenue doit être poreuse afin de permettre sa réduction par le monoxyde de carbone. Le grillage est réalisé vers 1000°C, SO2 est récupéré pour produire H2SO4. La réaction principale est la suivante :
PbS + 3/2 O2 = PbO + SO2 ΔrH°298 = – 416 kJ/mole
Le procédé le plus utilisé dans le monde consiste à effectuer le grillage sur des machines Dwight-Lloyd qui se présentent comme une bande sans fin de chariots mobiles munis de grilles, glissant sur des caissons étanches. L’air est soufflé à travers les grilles. Afin de décomposer PbSO4 qui se forme au cours du grillage, la température de grillage doit dépasser 950°C. Lors du grillage il se forme également une faible quantité de plomb fondu, qui reste dans le concentré, selon les réactions :
PbS + 2 PbO = 3 Pb + SO2 ΔrH°298 = + 320 kJ/mole
PbS + PbSO4 = 2 Pb + 2 SO2 ΔrH°298 = + 408 kJ/mole
La réaction de grillage étant très exothermique, il faut éviter une teneur trop importante en combustible (PbS) qui entraînerait une élévation trop importante de la température. Il ne faut pas atteindre 1114°C, température de fusion de PbS, ce dernier, à l’état fondu, ne pouvant plus être grillé. Pour cette raison la teneur des concentrés qui est, comptée en soufre, de 10 à 14 % est abaissée à une teneur moyenne de 6 % en ajoutant des concentrés préalablement grillés. Une partie du concentré grillé est donc recyclée en amont du grillage.
L’épaisseur de la couche grillée est de l’ordre de 30 cm, la surface de 50 à 90 m2, la vitesse de défilement d’environ 1 m/min, le débit d’air de 15 à 40 m3/min/m2.
Réduction : par pyrométallurgie entre 500 et 1000°C.
PbO + CO = Pb + CO2
CO2 + C = 2 CO
Avant réduction, le minerai est aggloméré et additionné de coke (180 kg/t de Pb) et de fondants, les ajouts de fondant intervenant souvent lors du grillage. La réduction a lieu selon 2 types de procédés :
- Au four à cuve, selon le principe du haut fourneau. Le four est rectangulaire, avec souvent un refroidissement extérieur par circulation d’eau (water jacket). Les 3/4 du plomb de Metaleurop à Noyelles-Godault étaient produits selon ce procédé, la production atteignait jusqu’à 350 t/jour.
- Imperial Smelting (ISP) qui permet de traiter des minerais mixtes Pb-Zn et de produire simultanément les deux métaux. Le four est de type haut-fourneau. Le plomb d’œuvre fondu sur lequel surnagent les scories est récupéré dans le bas du four. Les vapeurs de zinc (température d’ébullition : 907°C) qui doivent être condensées le plus rapidement possible pour éviter leur oxydation sont absorbées dans des condenseurs par une pluie de plomb à 440°C. Dans les condenseurs, la température du plomb liquide s’accroît jusqu’à 550°C. Le plomb zingueux obtenu est refroidi vers 440 °C. Les différences de solubilité et de densité, entre ces deux températures, permettent de séparer les deux métaux. Il faut faire circuler une quantité de plomb de l’ordre de 420 fois la quantité de zinc récupéré. Ce procédé était utilisé par Metaleurop à Noyelles-Godault pour 1/4 de la production et des capacités annuelles de 90 000 t de zinc et 35 000 t de plomb.
Le plomb d’œuvre obtenu selon ces deux procédés titre 98,5 %. Un raffinage est nécessaire.
Procédés en une seule étape : Kivcet, QSL, Isasmelt
Ils consistent à réaliser, dans le même réacteur, le grillage et la réduction, le grillage apportant la chaleur nécessaire à la réduction. Ils utilisent du dioxygène pur ou de l’air enrichi en dioxygène pour le grillage. Le bilan énergétique est nettement amélioré, l’étape de frittage sur machine Dwight-Lloyd est inutile, la teneur des gaz émis est élevée en dioxyde de soufre permettant ainsi une transformation plus aisée en acide sulfurique et une pollution atmosphérique moindre.
Le procédé Kivcet a été mis au point en Union Soviétique pour traiter, en 1971, un minerai Cu-Zn kazakh puis en 1985 un minerai Zn-Pb. La fonderie de Trail, au Canada, d’une capacité de 120 000 t/an de plomb, exploitée par la société Teck, utilise, depuis 1997, ce procédé. Un mélange de concentré de plomb, matières recyclées, charbon et coke, silice et argile, est introduit dans la chambre d’oxydation en présence de dioxygène. Les sulfures sont transformés en oxydes qui en présence des fondants introduits (silice et argile) donnent un bain semi-fondu qui percole au travers d’une couche de coke où l’oxyde de plomb est réduit en donnant du plomb fondu. Les matériaux obtenus, laitier et plomb passent ensuite dans une chambre où la fusion totale et la séparation laitier-plomb est achevée. Dans cette chambre, l’énergie est apportée par des électrodes de graphite. Un gaz contenant environ 15 % de dioxyde de soufre est refroidi, purifié et envoyé à la production d’acide sulfurique. A Trail, le passage du procédé classique au procédé Kivcet a permis de diminuer de 127 à 1,6 t/an les émissions atmosphériques de plomb.
Le procédé QSL (Queneau-Schumann-Lurgi) consiste à alimenter par un mélange aggloméré de concentré de plomb, matières à recycler, charbon ou coke et fondants (argiles et silice) un four horizontal légèrement incliné (0,5 % de pente), comportant deux zones, l’une d’oxydation, l’autre de réduction. La fonderie de la société Berzelius, du groupe Eco-Bat Technologies, à Stolberg, en Allemagne, produit ainsi, depuis 1990, 155 000 t/an de plomb, 100 000 t/an d’acide sulfurique et 700 t/an d’argent. Par rapport au procédé classique, la consommation d’énergie est passée de 15,2 à 4,5 GJ/t de Pb. Le four possède un diamètre de 3,5 m dans la zone d’oxydation et 3 m dans la zone de réduction pour une longueur de 33 m. Dans la zone d’oxydation, à 1000°C, alimentée en dioxygène pur par des tuyères plongeant dans le bain fondu, du plomb fondu se forme et est évacué. Le laitier, riche en oxyde de plomb passe, à contre courant dans la deuxième zone où il est réduit, vers 1250°C, à l’aide d’une injection de charbon finement divisé. Le plomb formé coule vers la chambre d’oxydation où il rejoint le plomb obtenu lors de la première étape. Le laitier est évacué du côté de la chambre de réduction. Les gaz produits sont refroidis à 400°C, purifiés et le dioxyde de soufre est transformé, par le procédé de contact, en acide sulfurique.
Le procédé Isasmelt, proposé par Glencore, a été développé à Mount Isa (Australie) où il a fonctionné de 1991 à 1995. Il est employé également dans le traitement pyrométallurgique des concentrés de cuivre. A Quijing, en Chine, le groupe Yunnan Metallurgical produit ainsi, depuis 2005, 80 000 t/an de plomb. Le procédé consiste à agglomérer le concentré de plomb, les matières à recycler et le fondant (argile, silice…) qui sont introduits dans un four vertical (4 m de diamètre pour 11 m de hauteur) contenant un bain fondu de laitier. La fusion du bain est obtenue à l’aide d’une lance immergée alimentée en air enrichi en dioxygène et en charbon pulvérisé. Une oxydation rapide a lieu avec formation de PbO qui réagit, en partie, avec PbS restant pour donner du plomb liquide. Plus de 40 % du plomb est ainsi récupéré. Le plomb restant, sous forme de PbO est récupéré dans le laitier dont une partie est prélevée régulièrement. Ce laitier est réduit ensuite de façon classique dans un haut-fourneau.
Raffinage
Il est soit pyrométallurgique (environ 80 % de la production), soit électrométallurgique (environ 20 % de la production).
Pyrométallurgique : par purifications successives du plomb à l’état liquide. Il consiste en un décuivrage en présence de soufre, une élimination de As, Sn et Sb, par oxydation à l’aide de nitrate de sodium (procédé Harris), une désargentation en présence de Zn (procédé Parkes), un débismuthage en présence de Ca et Mg (procédé Kroll-Betterton). Les divers sous-produits sont récupérés lors de ces opérations. Par exemple, pour une tonne de Pb peuvent être récupérés : 6 kg de Sb, 4 kg de Cu, 3,5 kg de As, 2 kg de Bi, 1 kg de Ag, 0,3 kg de Sn.
Le plomb obtenu appelé plomb doux à une teneur de ,99,99 %. Il est coulé en lingots de 45 kg appelés saumons.
Électrométallurgique : par électrolyse à anode soluble. Il est utilisé pour le plomb d’œuvre contenant plus de 2 % d’impuretés autres que le cuivre et lorsqu’on désire obtenir du plomb à faible teneur en bismuth (< 10 g/t de Pb), le procédé pyrométallurgique donnant couramment 100 g de Bi/t de Pb. L’électrolyte est généralement de l’acide fluosilicique (H2SiF6). La cathode est en plomb pur de 12 mm d’épaisseur, l’anode (200 kg) en plomb d’œuvre préalablement décuivré. La durée de l’électrolyse est de 4 à 8 jours, à 40-50°C, sous 0,3 à 0,5 V, avec une densité de courant de 150 A/m2, la consommation électrique est de 150 kWh/t de Pb.
Recyclage
Ou métallurgie de deuxième fusion ou d’affinage
L’obtention du métal a lieu à partir de la récupération de déchets, les batteries constituant la part la plus importante. Celle-ci est, en 2019, de 93 % aux États-Unis.
Le taux de récupération du plomb est important (59,9 % de la consommation, en 2019) car il est facile de récupérer le plomb des batteries. En France, la quasi totalité du plomb utilisé dans les batteries est récupéré.
Aux États-Unis, en 2019, 73 % de la consommation provient du recyclage. A côté d’une seule fonderie primaire, fermée fin 2013, il y a environ 20 fonderies secondaires dont 12 produisant plus de 30 000 t/an et représentant plus de 95 % de la production.
Composition moyenne (en masse) d’une batterie :
Sulfate de plomb |
24,5 % |
|
Oxyde de plomb |
16 % |
H2SO4 |
24 % |
|
Polypropylène |
7,7 % |
Alliage de plomb |
21 % |
|
PVC |
3,8 % |
Principe de la récupération des batteries :
- Casse des batteries, puis triage des sels de plomb, alliages de plomb, polypropylène qui est recyclé. Le polypropylène recyclé est destiné, à 50 % à des pièces automobiles (bacs de batteries), à 30 % à des conteneurs horticoles, à 10 % à des batteries.
- Réduction des oxydes par CO à 800-1200°C, déchloration par Na2CO3, désulfuration par Fe, dans des fours réverbère, à cuve ou rotatif.
- Obtention de plomb d’œuvre contenant 0,2 à 10 % de Sb, 200 à 400 g Cu/t, 200 à 800 g Sn/t.
- Un raffinage donne du plomb doux à 99,97 % ou des alliages (Pb-Sb, Pb-Sb-As, Pb-Sb-Sn…).
Une partie du recyclage est réalisé dans les fours de réduction de première fusion en même temps que le traitement des concentrés de plomb.
Le principal producteur européen de plomb recyclé est le groupe Eco-Bat Technologies, voir plus loin.
La société Recylex est le deuxième producteur européen. En France, les batteries sont récupérées et cassées à Escaudœuvres (59) et Villefranche-sur-Saöne (69). Le polypropylène est conditionné à Villefranche-sur-Saöne, le plomb et les sels de plomb sont traités par pyrométallurgie dans l’usine de la société à Nordenham, en Allemagne. En 2019, le traitement des batteries a fourni 105 260 t de plomb et 12 500 t de polypropylène.
Le groupe suédois Boliden, est, en Europe, un producteur important de plomb recyclé avec ses installations métallurgiques de Bergsöe qui a traité, en 2018, 67 000 t de batteries et produit 47 000 t d’alliages de plomb à partir de plomb recyclé.
Productions métallurgiques
En 2019, 1ère et 2ème fusion et ( ) 2ème fusion, en 2016. Monde : 11,752 millions de t (5,850 millions de t), Union européenne : 1,011 million de t (1,342 million de t).
en milliers de t
Chine |
4 908 (1 663) |
|
Allemagne |
315 (222) |
États-Unis |
1 157 (1 110) |
|
Royaume Uni, en 2017 |
313 (157) |
Corée du Sud |
810 (390) |
|
Canada |
246 (132) |
Inde |
650 (386) |
|
Japon |
238 (114) |
Mexique |
446 (230) |
|
Kazakhstan, en 2014 |
131 |
Sources : ILZSG, USGS et Ressources naturelles Canada
Aux États-Unis, la production de plomb de première fusion, avec 114 000 t en 2013, était assurée par une seule usine pyrométallurgique, qui a fermé fin 2013, exploitée depuis 1892, par Doe Run, à Herculaneum, dans le Missouri.
Au Canada la production de plomb de première fusion a été assurée par 3 usines avec, en 2018, une production de 115 247 t et celle de deuxième fusion par 4 usines avec une production de 140 008 t.
Les concentrés de plomb produits par les mines exploitées par Boliden, en Suède et en Irlande, ne sont qu’en partie traités par le groupe dans ses installation métallurgiques de Rönnskär, avec une production, en 2019, de 26 000 t de plomb, le reste étant livré à des producteurs européens.
En France toute production de première fusion a cessé avec l’arrêt de l’usine Metaleurop de Noyelles-Godault, en mars 2003.
Producteurs : principaux groupes mondiaux hors Chine.
- Eco-Bat Technologies exploite 29 usines, aux États-Unis, en Afrique du Sud et en Europe avec une capacité de production de 840 000 t/an de plomb, à 80 % de plomb recyclé et 500 t/an d’argent.
La production de plomb primaire et secondaire est assurée par 13 fours, dont 3 aux États-Unis, un en Afrique du Sud et 9 en Europe situés :
- En Allemagne, avec une usine de plomb primaire exploitée par la filiale Berzelius, à Stolberg, qui produit 155 000 t/an et deux usines de production de plomb secondaire situées à Braubach, avec 40 000 t/an et Freiberg avec 50 000 t/an.
- En Italie, avec deux usines qui produisent du plomb secondaire à Paderno Dugnano et Marcianise avec 70 000 t/an.
- En France, avec trois usines qui produisent du plomb secondaire à Toulouse (31), Bazoches-les-Gallerandes (45) et Pont Sainte Maxence (60) avec 60 000 t/an de plomb secondaire.
- Au Royaume Uni, avec une usine, à Matlock, qui produit 80 000 t/an de plomb secondaire.
- En Autriche, avec une usine, à Arnoldstein, qui produit 25 000 t/an de plomb secondaire.
En Europe, 2 usines produisent des laminés de plomb, au Royaume Uni à Welwyn Garden City, avec une capacité de production de 60 000 t/an et en France, à Estrée Saint Denis (60) avec Le Plomb Français et une capacité de 22 000 t/an.
- Glencore : 222 100 t, en 2019. Les usines de production sont situées :
- Au Kazakhstan, avec 69,61 % de la société Kazzinc qui exploite une fonderie à Ust-Kamenogorsk, selon le procédé Isasmelt, avec une capacité de production de 144 000 t/an et une production, en 2019, 31 600 t pour la part attribuée à Glencore.
- En Europe, au Royaume Uni, à Northfleet, selon le procédé Isalmelt, avec une capacité de production de 30 000 t/an de plomb secondaire et en Italie à Portovesme, en Sardaigne, selon le procédé Kivcet, avec une capacité de production de 85 000 t/an et un total de 190 500 t de plomb produites en Europe, en 2019.
- Korea Zinc, en Corée du Sud, à Onsan, a produit, en 2019, 413 000 t de plomb, en utilisant un procédé DRS, proche du procédé QSL.
- Nyrstar (Australie) : 160 000 t, en 2018, à Port Pirie, en Australie.
- Hindustan Zinc (Inde), détenu à 64,9 % par le groupe Vedanta : 197 838 t, en 2019, produites dans le Rajasthan, à Chanderiya avec une capacité de production de 85 000 t/an et Dariba avec une capacité de production de 120 000 t/an.
- Doe Run (États-Unis) : en décembre 2013, la production primaire à Herculaneum a cessé après avoir produit 124 900 t en 2013. Une production secondaire est effectuée à Boss, dans le Missouri, avec une capacité de production de 160 000 t/an.
- Recylex (France, Allemagne) : 105 260 t, en 2019, à Nordenham, en Allemagne.
- Teck (Canada) : 69 000 t, en 2019, à Trail, en Colombie Britannique.
Commerce international : en 2019.
Principaux pays exportateur de plomb brut sur un total mondial de 3,115 millions de t, en 2018.
en milliers de t de métal brut
Corée du Sud |
351 |
|
Allemagne |
130 |
Canada |
252 |
|
Malaisie |
85 |
Australie |
251 |
|
Kazakhstan |
81 |
Inde |
179 |
|
Russie |
80 |
Belgique |
155 |
|
Bulgarie |
80 |
Les exportations de la Corée du Sud sont destinées à 26 % au Vietnam, 20 % à l’Inde, 16 % aux États-Unis, 13 % à la Chine.
Principaux pays importateurs de plomb brut sur un total mondial de 3,222 millions de t, en 2018.
en milliers de t de métal brut
États-Unis |
503 |
|
Royaume Uni |
172 |
Inde |
223 |
|
Turquie |
126 |
Vietnam |
221 |
|
Corée du Sud |
126 |
Allemagne |
202 |
|
Espagne |
117 |
Chine |
182 |
|
Thaïlande |
106 |
Les importations des États-Unis proviennent à 49 % du Canada, 20 % du Mexique, 15 % de Corée du Sud.
Situation française
Production métallurgique : 54 939 t de plomb de 2ème fusion, en 2017.
Usines métallurgiques de production de plomb de 2ème fusion :
Commerce extérieur : en 2019.
Plomb d’œuvre :
- Exportations : 141 t vers la Pologne à 66 %, la Belgique à 34 %.
- Importations : 1 958 t de Belgique à 36 %, du Venezuela à 34 %, du Chili à 18 %, de Cuba à 9 %.
Plomb affiné brut :
- Exportations : 41 859 t vers l’Allemagne à 49 %, l’Espagne à 43 %.
- Importations : 35 380 t du Royaume Uni à 63 %, de Belgique à 26 %, d’Italie à 7 %.
Alliages plomb-antimoine :
- Exportations : 6 071 t vers l’Allemagne à 68 %, la Thaïlande à 19 %, la Hongrie à 8 %.
- Importations : 19 963 t du Royaume Uni à 71 %, de Belgique à 29 %.
Utilisations
Consommations mondiales
En 2019. Monde : 11,744 millions de t, Europe : 1,977 million de t.
en milliers de t
Chine |
4 887 |
|
Inde |
611 |
États-Unis |
1 632 |
|
Japon |
253 |
Corée du Sud |
611 |
|
|
|
Source: ILZSG
Secteurs d’utilisation
En 2018, dans le monde.
Accumulateurs |
80 % |
|
Munitions |
3 % |
Produits laminés et extrudés |
6 % |
|
Alliages |
2 % |
Pigments |
5 % |
|
Gaînes de câbles électriques |
1 % |
Source : Ressources naturelles Canada
En 1960, la part des accumulateurs était de 28 %.
Aux États-Unis, en 2017, plus de 85 % de la consommation du plomb est destinée aux accumulateurs, 5 % à la fabrication de munitions, 2 % à celle de produits laminés et extrudés, 1 % à la fabrication de produits moulés, 1 % à celle d’oxyde.
Accumulateurs : vu l’importance de la part des accumulateurs, la consommation de plomb est liée à la production automobile (parc automobile mondial : 500 millions de véhicules). Marché mondial annuel : 250 millions de batteries (9 millions en France pour le démarrage, dont 3,2 millions en premier équipement). En 10 ans, la durée de vie des batteries a été multipliée par 2 (de 3 à 4 ans en moyenne, actuellement) et la quantité de plomb utilisé a diminué de 12 à 8 kg.
Les batteries pour usage « stationnaire » sont conçues pour durer 25 ans.
En Amérique du Nord, en 2015, consommation de 127 millions de batteries, à 83,5 % destinées au remplacement de batteries usées, renfermant 1,2 million de t de plomb soit une moyenne de 9,84 kg de Pb/batterie.
En 2015, dans le monde, les batteries au plomb sont destinées à 58 % aux automobiles, 18 % aux vélos électriques (surtout en Chine), 8 % aux véhicules de traction électriques (chariots élévateurs…), 7 % aux télécom, 5 % sous forme de batteries scellées, 4 % comme batteries stationnaires utilisées en appoint du réseau électrique (hôpitaux, …).
Principe de fonctionnement :
A la plaque positive :
PbO2 + SO42- + 4H+ + 2e = PbSO4 + 2H2O avec un potentiel standard E° = + 1,685 V
A la plaque négative :
Pb + SO42- = PbSO4 + 2e avec un potentiel standard E° = – 0,356 V
Les cellules de 2 V sont connectées en série. La matière active est préparée sous forme de pâte constituée de poudre très fine (< 5 µm) d’oxyde de plomb, de plomb (20 à 30 %), d’acide sulfurique et d’eau, transformée par électrolyse en dioxyde de plomb à la plaque positive et en plomb spongieux à la plaque négative.
La matière active est déposée sur des grilles en alliage de plomb. L’alliage traditionnel (4 à 5 % de Sb) a de bonnes qualités mécaniques, mais Sb de la grille positive a tendance à passer en solution et à se redéposer sur la plaque négative. La surtension moindre de Sb/Pb entraîne un dégagement de H2 qui décharge la batterie (autodécharge) et consomme de l’eau. L’alliage Pb-Ca permet d’éviter la consommation d’eau mais du fait de la formation d’une couche passive sur la plaque positive gênant la charge de la batterie après décharge complète, cet alliage n’est utilisé que pour la grille négative. La grille positive est en alliage à 2 % de Sb.
L’électrolyte est de l’acide sulfurique à 4 à 5 moles/L. Les matériaux des séparateurs entre compartiments + et -, en papier cellulosique imprégné de PVC, sont de plus en plus remplacés par des fibres de verre ou du polyéthylène poreux, afin de diminuer la résistance interne de la batterie.
Le plomb représente 1/5 du prix d’une batterie.
On assiste au développement de grosses batteries destinées à réguler les réseaux de distribution électrique : 2 500 t de plomb dans des batteries, à Los Angeles, pour une puissance électrique de 400 MW.
Alliages : les éléments d’addition peuvent permettre d’abaisser le point de fusion de plomb, d’augmenter les propriétés mécaniques ou d’améliorer les caractéristiques électrochimiques :
- alliages pour soudure « à l’étain » : (62 % Sn, 32 % Pb, température de fusion : 183°C). Par exemple, une lampe à incandescence demandait 300 mg de plomb pour les soudures du culot. En France, la consommation dans ce domaine était de 75 t/an avant la fin programmée de ce type de lampe.
- alliages pour grilles de batteries : ajout de 2 % de Sb.
Revêtement des câbles électriques : le plomb est utilisé pour les câbles sous marins haute tension car il est parfaitement imperméable aux liquides.
Bâtiment : en France, consommation d’environ 2 000 t/an de feuilles de plomb pour l’entretien et la rénovation des monuments historiques. Utilisé comme matériau de couverture et de décoration pour la rénovation du dôme des Invalides à Paris. Le plomb est également utilisé en insonorisation, particulièrement basse fréquence et comme matelas antivibrations. Utilisation de 10 000 t/an comme accessoires de couverture (souches de cheminées, chenaux, recouvrement de balcons).
Notre-Dame de Paris avait sa toiture recouverte de 210 t de plaques de plomb de 5 mm d’épaisseur et 250 t étaient présentes dans la flèche construite par Viollet le Duc. Lors de l’incendie du 15 avril 2019, des températures comprises entre 600 et 900°C ont été atteintes et le plomb a fondu et, en partie, été volatilisé. La plus grande partie s’est retrouvée à l’intérieur de la cathédrale mais une fraction a été dispersée dans l’environnement, sous forme de poussière, autour de l’édifice.
Oxydes : PbO (litharge), Pb3O4 (minium), voir également le paragraphe verres au plomb.
- Les plaques positives des accumulateurs sont constituées d’une grille en alliage de plomb sur laquelle est déposée du dioxyde de plomb (PbO2). La litharge est utilisée, en partie, pour la fabrication de cet oxyde qui se forme lors de la première charge de la batterie.
- Utilisés sous forme de litharge comme stabilisant du PVC (qui contient 1 % d’oxyde de plomb) lorsqu’il est employé de façon durable (bâtiment…). Toutefois, dans l’Union européenne, cette utilisation est terminée depuis 2015.
- Dans la fabrication des céramiques : le minium, utilisé dans les glaçures, sert d’opacifiant en formant un silicate. De 70 à 90 % de l’oxyde utilisé dans ce secteur est employé à la fabrication de carrelages (59 g de PbO/m2).
- Les pigments, élaborés à partir de litharge : jaune (chromate : PbCrO4 entrant dans la fabrication de la peinture des ex-bandes jaunes routières), rouge (molybdate : PbMoO4) ne sont plus utilisés.
- Le minium a été pendant longtemps utilisé comme peinture antirouille. Il est de moins en moins employé, l’appellation « minium » ayant été conservée pour des produits antirouille qui ne contiennent pas d’oxyde de plomb.
Verres au plomb : l’oxyde de plomb augmente l’indice de réfraction des verres qui de n = 1,5, peut atteindre n = 1,8. Les verres de cristal ont des teneurs exprimées en PbO d’au moins 24 %. Des fibres optiques sont constituées d’une peau en verre ordinaire (n = 1,5) et d’un cœur en verre au plomb (50 % de PbO) d’indice 1,62.
Le numéro atomique élevé du plomb en fait le meilleur élément pouvant entrer dans la composition de verres de protection contre les rayonnements (X et nucléaires). Le verre du cône des tubes de télévision contenait jusqu’à 30 % de PbO, soit 1 kg de plomb par téléviseur couleur. Ce verre brunissant sous l’impact des rayons X, le verre de l’écran contenait des oxydes de strontium et baryum, éléments possédant également des numéros atomiques élevés. L’usine de retraitement des combustibles irradiés de La Hague utilise plus de 200 fenêtres de verre au plomb (jusqu’à 80 % de PbO). Les fenêtres sont formées par des dalles de verre collées les unes aux autres. L’épaisseur peut atteindre 1,2 m et la masse, plusieurs tonnes.
Plomb de chasse : l’alliage (1,5 % Sb, 0,8 % As), est fabriqué selon le procédé « de la tour ». Par exemple, entre 1824 et 1836, la tour Saint Jacques à Paris a été utilisée pour produire du plomb de chasse. Il en a été de même à Rouen pour la tour Saint André.
Pollution de l’atmosphère et toxicité
Pollution de l’atmosphère par le plomb : d’après pour la Science n°228.
L’étude de la composition en plomb de carottes glaciaires prélevées au Groenland a montré que celle-ci a varié de 0,5 pg (10-12 g) de plomb par g de glace en l’an – 1000 à 2 à 3 pg entre – 500 et 200 pour attendre 10 pg vers 1770, 50 pg vers 1900, 100 pg vers 1969 pour décroître ensuite à environ 10 pg après la quasi-disparition d’abord aux États-Unis et au Japon de l’essence contenant des additifs à base de plomb. La pollution à l’époque romaine et jusqu’au début du XXème siècle est principalement due au fonctionnement des fours de réduction qui, à l’époque romaine, rejetaient dans l’atmosphère jusqu’à 5 % de la production soit 4 000 t/an à l’apogée de l’Empire romain. Depuis 1923 et l’utilisation de l’essence plombée, ce sont le plomb tétraéthyle et tétraméthyle qui transformés en plomb triéthyle et diéthyle ont été les principaux polluants de l’atmosphère.
Toxicité :
Le saturnisme est une maladie liée à une intoxication aiguë ou chronique au plomb. Incorporés dans l’organisme, les ions Pb2+ entrent en compétition avec Ca2+ dans la formation des os constitués de phosphate de calcium pour leur partie minérale. Le plomb peut aussi bloquer plusieurs enzymes. L’ingestion doit être limitée à 3 mg Pb/semaine.
Les normes de l’Union européenne sont pour l’eau potable d’un maximun admissible de 10 µg Pb/L depuis fin 2013 et d’une concentration maximale admissible dans l’atmosphère de 0,5 µg/m3, en moyenne annuelle.
La plombémie, taux de plomb dans le sang, varie, en général, de 7 à 20 µg/100 mL de sang, en fonction de la contamination atmosphérique (0,1 à 0,2 µg/m3 dans les zones rurales, 1 à 2 µg/m3 en moyenne dans les grandes villes). En Europe, la valeur maximale admissible est de 35 µg/100 mL. Chez l’enfant, 15 µg/100mL sont considérés comme une limite maximale.
La céruse (2PbCO3,Pb(OH)2) qui a été pendant longtemps employée comme pigment blanc dans les peintures est interdite d’usage par les professionnels dans ce secteur depuis 1948 mais elle reste présente dans des vieilles peintures et présente l’inconvénient d’avoir un goût sucré. Par ailleurs son interdiction de mise sur le marché ne date que de 1993 et l’interdiction définitive de son emploi de 2003. On évalue, en France, le nombre d’enfants en contact avec ces peintures à 140 000 dont la moitié dans l’Île de France. En 1988, à Paris, 2 enfants sont morts après avoir ingéré des vieilles peintures contenant de la céruse et de nombreux autres sont intoxiqués chaque année.
Bibliographie
- The International Lead and Zinc Study Group, rua Almirante Barroso 38, 5th Floor, Lisbonne, 1000 – 013, Portugal.
- The International Lead Association, Bravington House, 2 Bravingtons Walk, London, N1 9AF, Royaume Uni.
- A3M, 17 rue Hamelin, 75783 Paris Cedex 16.
- P. Blazy et El-Aïd Jdid, « Métallurgie du plomb : procédés classiques et ressources primaires », Techniques de l’Ingénieur, 2011.
- P. Blazy et El-Aïd Jdid, « Métallurgie du plomb : procédés modernes et sources secondaires », Techniques de l’Ingénieur, 2011.
- « Histoire de la production du plomb« , Wikipédia.
- G. Troly, « La Société Minière et Métallurgique de Peñarroya« , Réalités Industrielles, p27-34, août 2008.
- J.C. Michel, Économie du plomb, Eco-note, Ecomine, BRGM, juillet-août 2007.
- Pour la Science, n°228, octobre 1996.
Commentaires récents